One of the most frequent inquiries from those working with Nichrome wire is whether it can be soldered effectively.
This question arises due to the unique properties of Nichrome, a widely used material in various industrial and domestic applications.
Nichrome, an alloy of nickel and chromium, is renowned for its high resistance and durability, particularly in high-temperature environments. This blog with refer to Nichrome 80 (Ni80) for the phrase Nichrome.
It is a staple in the manufacturing of heating elements, resistors, and a range of electrical and electronic devices. This blog delves into the complexities of soldering Nichrome wire, exploring its feasibility, the challenges involved, and potential alternatives for effective wire joining.
Let’s get into it..
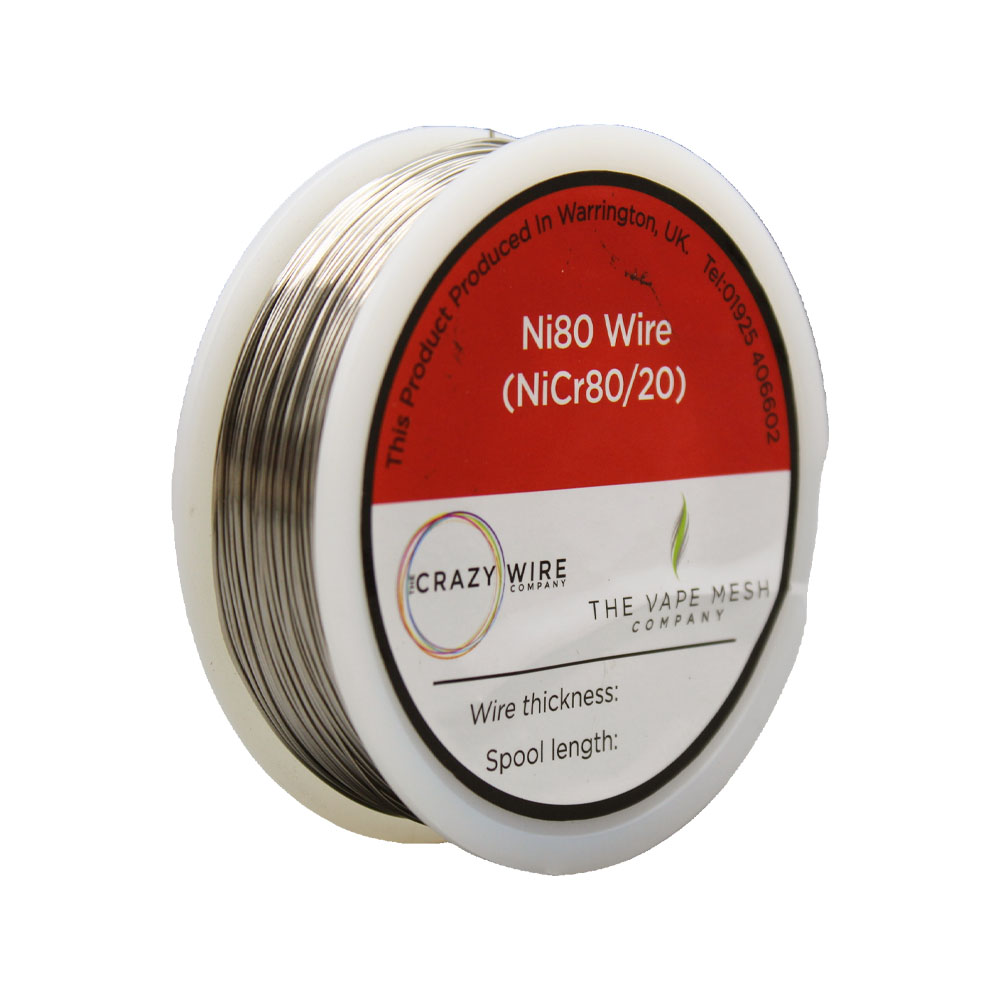
Understanding Nichrome Wire
In addition to being highly resistant to oxidation and stable at high temperatures, nickelchrome wire is also composed primarily of nickel (approx. 80%) and chromium (approx. 20%). As a result of these properties, it is ideal for applications that require consistent heat generation, such as toasters, hair dryers, and industrial furnaces. Further, its resistance properties are used in electrical resistors and other components that require controlled resistance.
Despite frequent thermal cycling, Nichrome wire’s high nickel content contributes to its corrosion resistance. On the other hand, chromium enhances the wire’s strength and heat resistance, allowing it to maintain structural integrity in challenging environments. These metals are combined to create a wire that is not only durable, but maintains a consistent resistance over time, an important factor in many electrical applications.
Challenges of Soldering Nichrome Wire
Due to its physical and chemical properties, Nichrome wire presents specific challenges when soldering. Its high melting point is one of its primary challenges. Due to Nichrome’s much higher melting point than standard solder, typical soldering processes may not provide enough heat to effectively join the wires. Furthermore, chromium creates an oxide layer on the wire’s surface, complicating the soldering process further. The oxide layer can prevent the solder from adhering properly to the wire, resulting in weak or ineffective joints.
Soldering Nichrome wire requires special consideration and techniques. Soldering isn’t just about the heat applied, but also about how the wire is prepared before and during the process. The key to achieving a successful and durable solder joint with Nichrome wire is understanding these nuances.
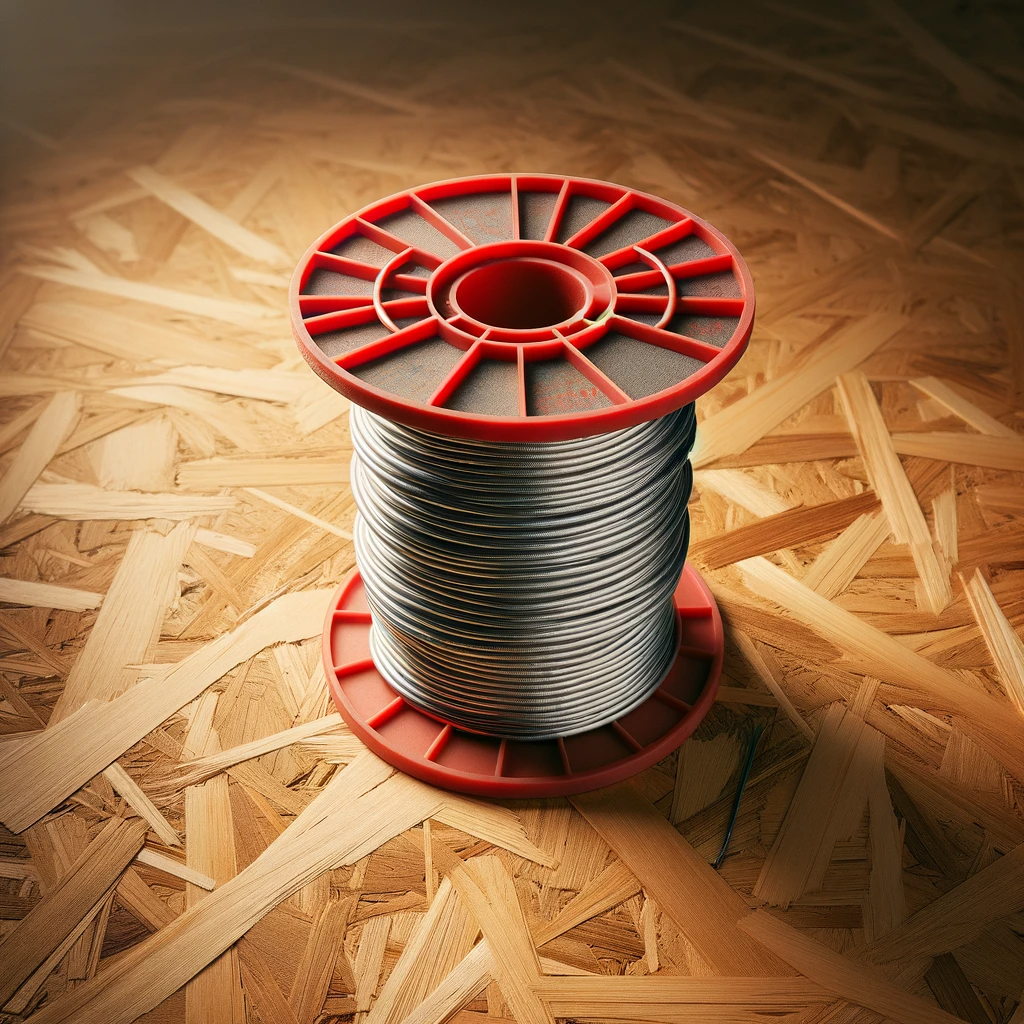
Soldering Techniques for Nichrome Wire
Soldering Nichrome wire can be challenging but not impossible. Here’s a guide on how to achieve effective soldering:
Prepare the Wire: Ensure that any oxide layer on the Nichrome wire is thoroughly removed by first cleaning it thoroughly. A wire brush or fine sandpaper can be used to gently abrade the surface.
Select the Right Solder: You should choose a solder with a high melting point, such as silver solder, which can withstand the heat required to solder Nichrome, such as silver solder.
Choose Appropriate Flux: Use a flux that is specifically designed for high-temperature applications. The flux will help remove oxidation from the solder and ensure a better bond between the solder and the Nichrome wire as well as removing oxidation from the solder.
Heating: Heat with a high-temperature soldering iron or torch. Nichrome’s high melting point requires a heat source that can reach and maintain a higher temperature than traditional soldering irons.
Soldering Process: Solder should be applied after the wire has been heated uniformly. Make sure the solder flows and covers the joint area completely.
Cooling: Allow the joint to cool naturally. Avoid quenching as it can lead to a brittle joint.
Inspection and Cleanup: Make sure that there are no gaps or weak spots in the joint. After the joint has cooled down, it is important to clean any flux residue left behind.
Alternative Methods to Join Nichrome Wire
While soldering is a common method, there are alternatives for joining Nichrome wire:
Mechanical Twisting: Wires are twisted together in this process. The connection may not be as secure and can have higher electrical resistance, but it’s fast and doesn’t require heating.
Crimping: It is possible to provide a strong mechanical bond by using crimp connectors. In addition to maintaining a consistent electrical connection, this method is reliable.
Conductive Adhesives: Nichrome wires can be bonded with these adhesives without the need for heating in order to achieve a good bond. Although they are useful in applications that are sensitive to heat, they may not be able to provide a connection that is as strong as soldering.
There is no doubt that each method has its benefits and disadvantages, and the choice has to be made based on the specific requirements of the application, such as strength, electrical conductivity, and heat resistance.
Case Studies and Practical Applications
Nichrome wire was successfully soldered to repair a heating element in a small appliance. High-temperature solder and appropriate flux made the repair durable and efficient.
Another example of a creative project involved the use of conductive adhesives to join Nichrome wires for a low-heat application using conductive adhesives. In order to avoid damaging the delicate components involved in this project, this method was chosen.
As these examples illustrate, soldering Nichrome wire can be a challenge depending on the techniques and materials you use, but with the right techniques and materials, it can be done successfully. In choosing the right method for a particular application, it is essential to balance factors like strength, conductivity, and thermal requirements with the application’s specific needs.
Safety Precautions and Best Practices
When working with Nichrome wire, especially during soldering, safety is paramount. Here are some essential precautions and best practices:
Wear Protective Gear: Wear safety glasses to protect your eyes from splatters and gloves to protect your hands from heat and sharp wire ends.
Ventilation: As a precaution, make sure that your workspace has proper ventilation, as fumes from soldering and flux can be harmful to your health if inhaled.
Handle with Care: As a result of the soldering process, Nichrome wire can become quite hot. It should be handled with care in order to avoid burns.
Use the Right Tools: The tools you use for high-temperature soldering should be specifically designed for that purpose. As a result, the soldering process is more effective and accidents are less likely to occur as a result.
Electrical Safety: To prevent electric shocks whilst working with Nichrome wire, make sure that all power sources are turned off before you start your work if you are working with Nichrome wire in electrical applications.
Proper Storage: Store Nichrome wire and tools properly after use to prevent accidental injury or damage.
Nichrome wire can be soldered with the right approach and understanding of its unique properties, although it is a challenge.
It requires careful attention to detail, the right soldering materials, and a thorough understanding of how to overcome its high melting point and oxide layer.
Understanding these nuances is crucial for those who wish to use Nichrome wire in their projects.
Available Nichrome Wire Options:
Ni80 | Ni80 | Ni90 | Ni90 | Ni60 | Ni60 |
Diameter (mm) | AWG | Diameter (mm) | AWG | Diameter (mm) | AWG |
0.05 | 44 | ||||
0.06 | 42 | ||||
0.07 | 41 | ||||
0.08 | 40 | 0.08 | 40 | ||
0.09 | 39 | ||||
0.1 | 38 | 0.1 | 38 | ||
0.12 | 36 | ||||
0.125 | 36 | ||||
0.13 | 36 | 0.13 | 36 | ||
0.14 | 35 | ||||
0.15 | 35 | ||||
0.16 | 34 | ||||
0.17 | 34 | ||||
0.18 | 33 | ||||
0.2 | 32 | 0.2 | 32 | ||
0.21 | 32 | ||||
0.23 | 31 | ||||
0.25 | 30 | 0.25 | 30 | 0.25 | 30 |
0.27 | 29 | ||||
0.28 | 29 | ||||
0.29 | 29 | ||||
0.3 | 29 | 0.3 | 29 | ||
0.32 | 28 | 0.32 | 28 | 0.32 | 28 |
0.35 | 28 | ||||
0.37 | 27 | 0.37 | 27 | ||
0.38 | 27 | ||||
0.4 | 26 | 0.4 | 26 | 0.4 | 26 |
0.42 | 26 | ||||
0.45 | 25 | 0.44 | 25 | ||
0.5 | 24 | 0.5 | 24 | 0.5 | 24 |
0.54 | 23 | ||||
0.6 | 22 | 0.6 | 22 | ||
0.64 | 22 | 0.64 | 22 | ||
0.7 | 21 | 0.72 | 21 | ||
0.8 | 20 | 0.81 | 20 | 0.8 | 20 |
0.9 | 19 | 0.9 | 19 | 0.9 | 19 |
1 | 18 | ||||
1.15 | 17 |
For more insights on working with Nichrome wire or to explore a wide range of high-quality materials, visit our website at www.wireandstuff.co.uk.
Whether you’re a seasoned professional or a beginner, our team is here to provide expert advice and top-notch Nichrome wire tailored to your project needs.
Contact us today to find the perfect solution for your wiring challenges.
We offer also a massive range of stainless steel wire and nichrome wire through our store. Choose the wire that you want to work with and we’ll get spooling.
If you’re interested in learning more about wire, check out our other blog on Everything You Need to Know About Wires.
We are also proud to supply this product on our highly popular eBay store, check us out there too.
Thank you for checking out our site.
- MULTIBUY SAVINGS – ORDER 5 FOR 20% OFF
- FREE UK Delivery For All Orders Over £25
- Immediate Express Dispatch From Stock
- Orders Fulfilled From Warrington, UK
- Tracked Delivery with Order Updates
- 30-Day Unused Returns Accepted
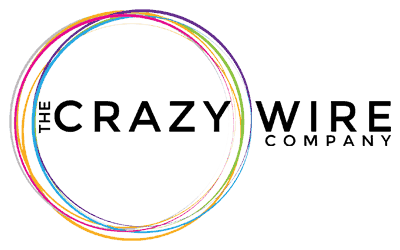
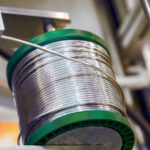
Nichrome Wire Safety: Top Tips for Working Safely
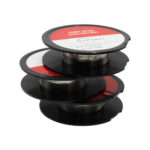
Best Wire for Electronics Projects
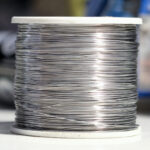
Is Ni80 Wire Suitable for DIY Heating Elements
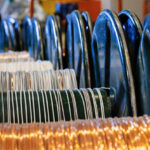
Wire Grades Explained
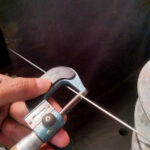
How Wire Diameter Affects Strength and Flexibility
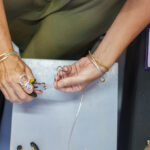
How to Cut and Shape Wire for Custom Applications
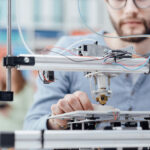
Can Wire Be Used in 3D Printing?
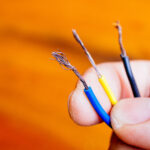
How Wire Composition Affects Conductivity
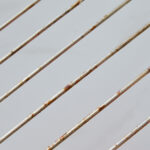