A wire’s suitability for high-temperature environments isn’t solely a matter of efficiency — it’s also a matter of safety.
With industries striving for innovation, from aeronautics to electronics, the demand for materials that withstand extreme temperatures has increased.
The question: “How Does This Wire Perform in High-Temperature Environments?” is one that we receive often. This is not simply a matter of endurance but also about the reliability and longevity of the entire system it supports.
This article embarks on a comparative analysis of various wires: nichrome, FeCrAl A1, stainless steel, copper, brass, and pure nickel, each revered in its own right for its high-temperature performance.
By dissecting their attributes, we aim to illuminate the decision-making process for engineers and manufacturers, ensuring the wire they choose meets the rigorous demands of their high-heat applications.
Why High-Temperature Performance Matters
In high-temperature environments, wires face numerous challenges. When a material is exposed to such conditions for an extended period of time, it may lose mechanical strength, become more brittle, or even undergo a chemical change, potentially resulting in a catastrophic failure. If you select a wire that cannot withstand the rigors of a high-temperature setting, you may experience product malfunctions and safety risks.
Wire materials must be resilient at high temperatures in industrial settings. Wires are often required to remain electrically and mechanically functional for long periods of time in these environments, despite prolonged exposure to heat that would normally degrade ordinary materials. Commercially, high-temperature wire is used in everyday products, emphasising the need for materials that are reliable and safe.
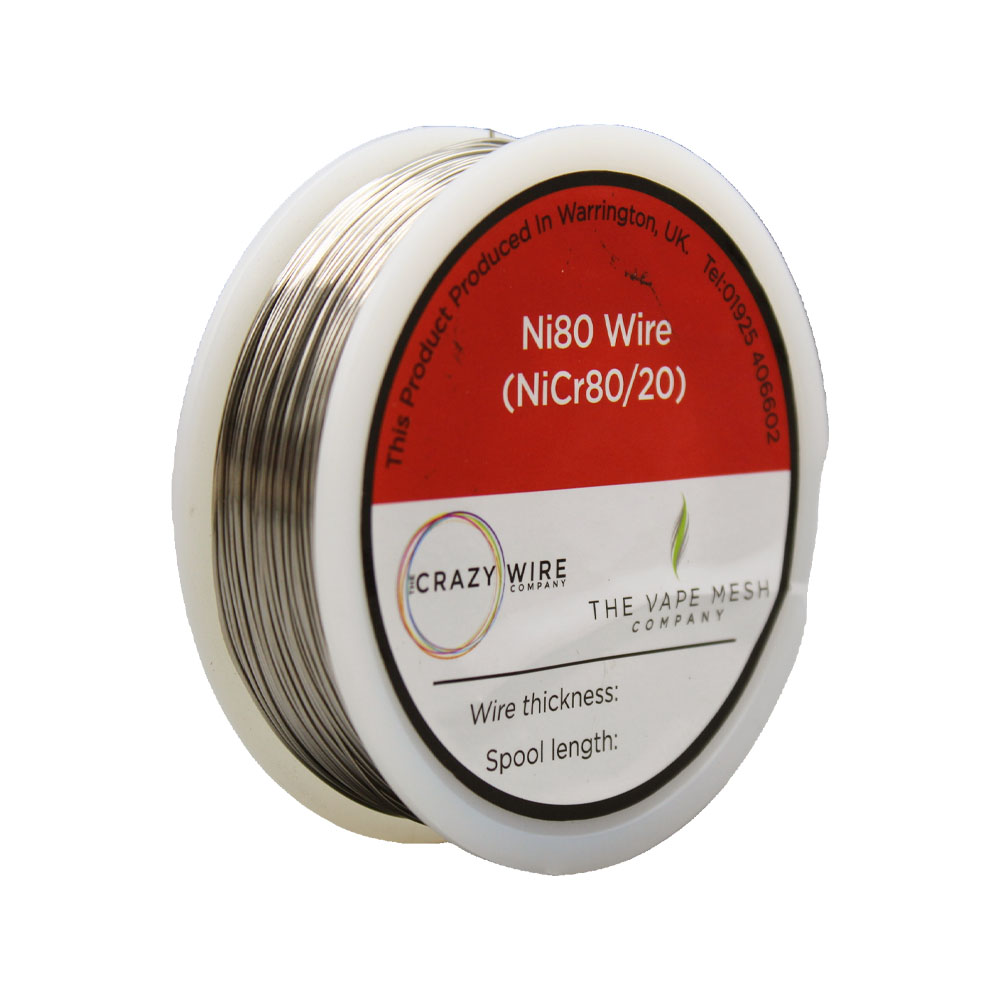
Nichrome Wire in High-Temperature Environments
Nichrome, an alloy of nickel and chromium, is exceptionally resistant to oxidation at high temperatures. In heat-resistant applications, such as appliances, industrial furnaces, and certain types of aerospace engineering, nichrome wire is typically composed of 80% nickel and 20% chromium.
Even under high-temperature conditions, nichrome maintains its structure and does not easily creep, keeping it dimensionally stable. The wire operates effectively at temperatures up to 1150°C (2100°F), making it ideal for applications with sustained heat.
However, nichrome does have its limitations. A high electrical resistivity makes it ideal for heating applications, but not necessarily for applications requiring efficient electrical conductivity. As temperatures rise, its strength decreases, which makes it more prone to deformation under load, even if it doesn’t melt.
Nichrome wire is typically used in toaster ovens, hair dryers, kilns, and industrial processes that require controlled heat. The wire’s performance in these environments is a testament to its reliability, but it’s crucial to match the wire’s capabilities with the application’s requirements to avoid material failures.
FeCrAl A1 Wire's Heat Resilience
FeCrAl wire, a name often synonymous with superior heat resilience, is an alloy composed predominantly of iron, chromium, and aluminum. FeCrAl wire is able to withstand and maintain structural integrity under extreme heat thanks to this blend. In high-temperature applications, FeCrAl can operate at temperatures up to 1400°C (2552°F), making it an indispensable material.
When heated, FeCrAl forms an aluminum oxide layer on its surface, which contributes to its heat-resistant properties. The layer acts as a protective barrier, preventing further oxidation and helping the wire retain its shape and strength at temperatures where other materials might fail. Unlike nichrome, FeCrAl A1 has a higher melting point and is more resistant to oxidation, allowing it to be used at high temperatures for a longer period of time.
FeCrAl A1’s industrial uses are extensive and varied. Electric furnace heating elements, kiln furniture, and ceramics and glass production all use it. Due to its resilience, the wire is suitable for heat treatment processes requiring sustained high temperatures to alter the properties of other metals. Additionally, FeCrAl is used to manufacture home appliances such as toasters and hair dryers, which require high levels of safety and durability.
As compared to nichrome, FeCrAl is able to operate at higher temperatures for longer periods without degradation. The choice between the two heating elements often depends on specific application requirements, including the maximum operating temperature and the level of resistance.
Stainless Steel Wire's Durability at Elevated Temperatures
There are numerous alloys of stainless steel wire, each designed to meet the needs of different environments. Due to their enhanced thermal properties, grades such as 310, 316, and 330 stainless steel are frequently used for high-temperature applications. The higher nickel and chromium content of these grades contributes both to their corrosion resistance and their ability to retain tensile strength at high temperatures.
Grade 310 stainless steel, for example, can withstand temperatures up to 1150°C (2100°F) and is commonly utilised in furnace parts, heat exchangers, and jet engine parts. The grade 316 offers a good balance between heat resistance and corrosion resistance, making it ideal for chemical processing equipment.
Stainless steel wire must perform consistently without experiencing thermal fatigue in heat-intensive applications. In settings ranging from cooking utensils to automotive exhaust systems, where high temperatures are frequently and cyclically encountered, it is used. With its durability in these conditions, the wire remains a reliable component for a long time.
Although stainless steel wire doesn’t have the same high-temperature resistance as FeCrAl or nichrome, it offers a broader range of properties, such as mechanical durability, chemical resistance, and overall material stability. Its performance in heat-intensive applications is not only determined by its resistance to high temperatures, but also by its ability to maintain its properties without significant corrosion or loss of strength, ensuring longevity and reliability.
Copper Wire: Conductivity vs. Heat Tolerance
Copper wire has exceptional electrical conductivity, second only to silver in its ability to conduct electricity. Electrical wiring, electronic components, and telecommunications use it because of its inherent characteristics. Due to copper’s atomic structure, electrons flow freely across its surface, facilitating efficient energy transfer.
However, when it comes to heat tolerance, copper wire presents a more nuanced profile. Copper has a melting point of approximately 1085°C (1985°F), which is relatively high, but lower than that of many specialised high-temperature wires. Copper can become malleable and lose strength at high temperatures, leading to deformation under load. Furthermore, prolonged exposure to high temperatures can cause oxidation, known as annealing, which can reduce its electrical conductivity.
Copper wires perform less well in high-temperature environments than FeCrAl A1 or nichrome wires. They are specifically designed to maintain structural integrity and performance at temperatures that would significantly alter copper’s properties. Heat sinks and other thermal management applications benefit from copper’s high thermal conductivity, which allows it to quickly transfer heat away from hot zones.
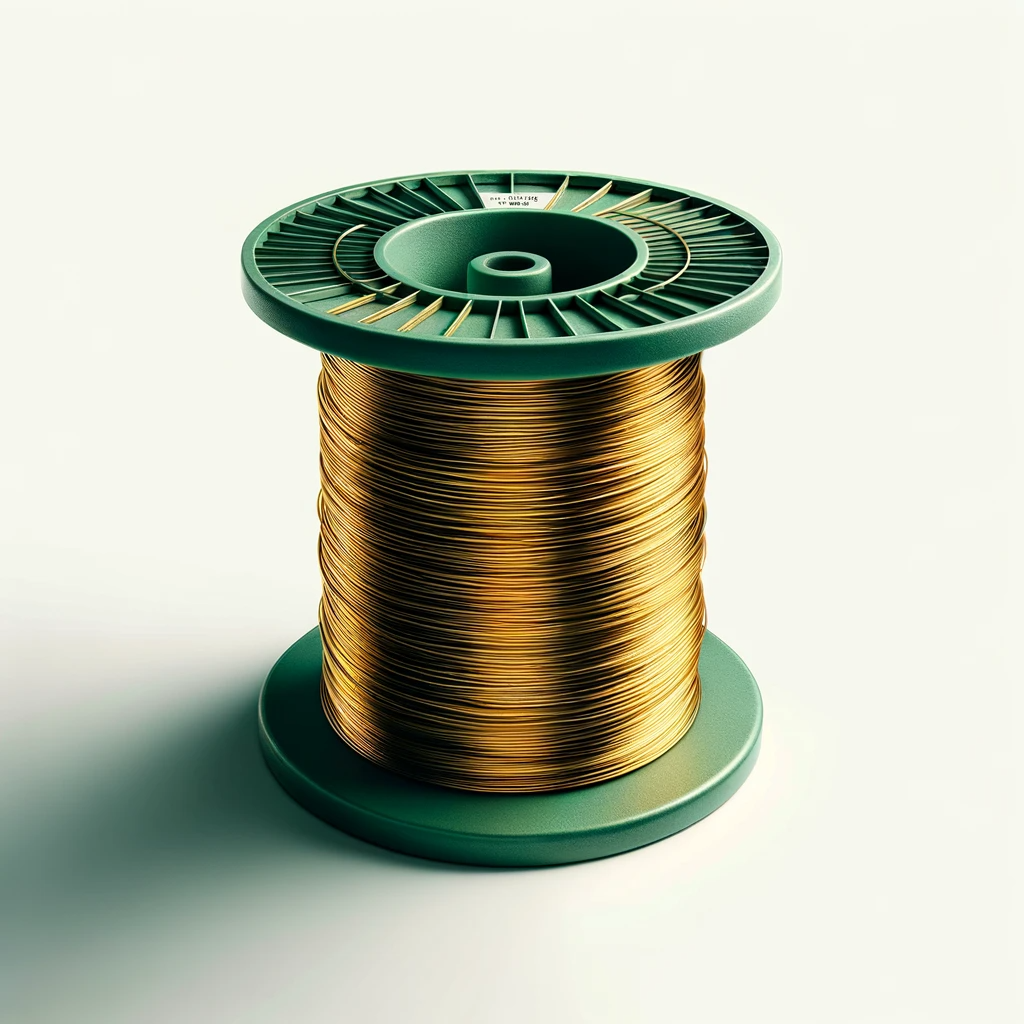
Brass Wire: Combining Strength and Thermal Conductivity
As an alloy composed primarily of copper and zinc, brass wire inherits a variety of properties. The properties of brass make it useful in applications that benefit from both strength and thermal conductivity. Due to its thermal properties, brass wire can withstand moderate temperatures while maintaining its tensile strength and form. Brass has a lower heat tolerance than metals like FeCrAl A1 or nichrome and is susceptible to deterioration at high temperatures.
In most cases, brass wire is used for its corrosion resistance, machinability, and aesthetic appeal rather than for its thermal properties. It is commonly used in musical instruments, decorative items, and electrical component casings. Brass wire is beneficial for heat performance in components like connectors and fasteners that require moderate heat resistance as well as electrical conductivity.
Pure Nickel Wire: The High-Temperature Contender
Nickel wire is a major player when it comes to high-temperature performance. As a result of its melting point around 1455°C (2651°F), it offers substantial heat tolerance, making it suitable for environments where many other metals would fail. Thermal stress allows it to retain its physical properties despite its resistance to oxidation at elevated temperatures.
As a result of its robust performance in extreme temperatures, pure nickel wire is often used in applications such as heating elements, thermocouples, and high-temperature battery terminals. Further contributing to its suitability for these demanding applications is its ductility and corrosion resistance. In settings where thermal resilience is paramount, pure nickel is often the material of choice in spite of its lower level of electrical conductivity than copper.
Choosing the Right Wire for High-Temperature Applications
Selecting the optimal wire for high-temperature applications requires a nuanced understanding of material properties and an assessment of the specific conditions the wire will encounter. Engineers and designers must consider several factors to ensure the chosen wire meets all operational demands:
Temperature Resilience: Compare the maximum temperatures the wire will be exposed to with the melting points and thermal degradation thresholds of different wire materials.
Electrical Conductivity: Determine the electrical requirements of the application. If high conductivity is essential, materials like copper may be preferred, unless the temperature conditions exceed the material’s safe operating limits.
Mechanical Strength: Make sure the wire can withstand the mechanical loads it will be subjected to. Stainless steel might be a good choice for applications requiring strength.
Corrosion Resistance: Take into account the environment in which the wire will be used. The performance of materials like nichrome, FeCrAl A1, or stainless steel is superior in corrosive environments.
Cost-Effectiveness: Achieve a balance between performance benefits and budgetary constraints, taking into account not just the initial costs but also the longevity and maintenance requirements.
We have produced a basic matrix that may be of assistance:
Criteria | Nichrome | Kanthal | Stainless Steel | Copper | Brass | Pure Nickel |
Temperature Resilience | High | Very High | High by grade | Moderate | Moderate | High |
Electrical Conductivity | Low | Low | Moderate | Very High | High | Moderate |
Mechanical Strength | Moderate | High | High | Moderate | Moderate | High |
Corrosion Resistance | High | High | High | Low | Moderate | High |
Cost-Effectiveness | Moderate | Moderate | Varies | Low | Moderate | High |
Wire selection for high-temperature environments can have a significant impact on a project’s success. There is a need to understand the unique performance characteristics of nichrome, FeCrAl A1, stainless steel, copper, brass, and pure nickel wires under such conditions. It is important to consider temperature resilience, conductivity, strength, and environmental resistance when choosing a material.
Contact The Crazy Wire Company for expert advice on choosing the right high-temperature wire. To ensure you find a wire that meets your specifications as well as exceeds your expectations, our specialists will guide you through the selection process.
Explore our wide range of wire options tailored for high-temperature applications on our website for detailed specifications.
Your project deserves the best; let us help you achieve it.
We offer also a massive range of stainless steel wire and nichrome wire through our store. Choose the wire that you want to work with and we’ll get spooling.
If you’re interested in learning more about wire, check out our other blog on Everything You Need to Know About Wires.
We are also proud to supply this product on our highly popular eBay store, check us out there too.
Thank you for checking out our site.
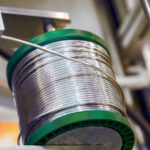
Nichrome Wire Safety: Top Tips for Working Safely
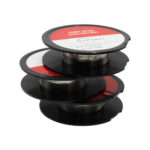
Best Wire for Electronics Projects
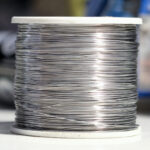
Is Ni80 Wire Suitable for DIY Heating Elements
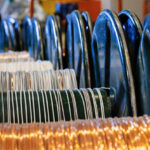
Wire Grades Explained
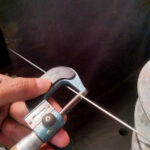
How Wire Diameter Affects Strength and Flexibility
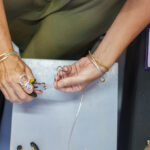
How to Cut and Shape Wire for Custom Applications
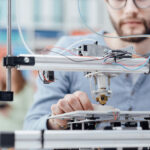
Can Wire Be Used in 3D Printing?
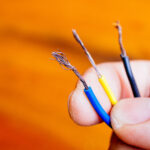
How Wire Composition Affects Conductivity
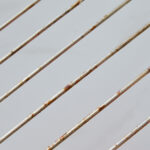