Choosing the right materials for specific applications is paramount for ensuring performance, safety, and cost-effectiveness. This is particularly true for high-temperature applications, including the specialised process of hot wire cutting.
A common inquiry in this context is “Can 316 Grade Wire Be Used as a Hot Cutting Wire?”
This question highlights the need for wires that can not only withstand high temperatures without degradation, but also retain their physical and mechanical properties under thermal stress.
High-temperature cutting applications can benefit from the robustness and corrosion resistance of 316 grade stainless steel, which is revered for its robustness and corrosion resistance. To provide a comprehensive analysis of 316 stainless steel’s capabilities as a hot cutting wire, we examine its characteristics, temperature tolerance, and performance in high heat environments.
Overview of 316 Grade Stainless Steel
316 grade stainless steel, also known as marine-grade stainless steel, consists primarily of iron, with chromium, nickel, and molybdenum as additives. Its inclusion of molybdenum, in particular, makes 316 more corrosion-resistant in chloride environments and more resilient under higher temperatures. Medical devices, food processing equipment, and marine hardware benefit from this grade of stainless steel’s exceptional strength and corrosion resistance.
316 stainless steel features excellent weldability and formability, as well as the ability to maintain integrity in environments prone to acid corrosion and high temperatures. A balanced composition ensures a stable internal structure, which resists scaling and remains strong even at temperatures up to 899°C (1650°F). In light of its durability, resistance, and thermal stability, 316 grade stainless steel is an excellent candidate for high-temperature applications, prompting further investigation into its feasibility as a hot cutting wire.
High-Temperature Applications of 316 Stainless Steel
316 stainless steel’s temperature resilience makes it a preferred material for applications that operate within a wide range of temperatures, especially those exceeding normal environmental conditions. Its ability to withstand continuous exposure to temperatures up to around 870°C (1600°F) and intermittent exposure up to 899°C (1650°F) without significant thermal degradation is a testament to its high-temperature capabilities. This thermal resistance is crucial for applications such as chemical processing equipment, heat exchangers, and exhaust manifolds, where materials are subjected to harsh thermal cycles.
In the context of hot wire cutting, the temperature limits and resilience of 316 stainless steel are of particular interest. Hot wire cutting involves passing an electric current through a wire to heat it, which then melts or vaporises the material to be cut, often foam or polystyrene. This process requires the wire to not only reach high temperatures but also to maintain those temperatures without losing tensile strength or flexibility. While traditionally nichrome or kanthal wires have been favored for their high resistivity and heat tolerance, the inquiry into 316 stainless steel suggests a potential for diversification in material choice, contingent on its performance under similar stress.
Hot Cutting Wire: Material Requirements
Hot cutting wires are specialised tools used in industries that require precision and the ability to cut materials at elevated temperatures. Electrically heated wires melt or vaporise the target material, providing a clean cut with minimal physical effort. The essential properties for hot cutting wires include:
- Heat Tolerance: Wires must withstand high temperatures without melting, deforming, or losing tensile strength. Throughout the cutting process, this ensures consistent performance.
- Electrical Resistance: When an electric current passes through a wire, high electrical resistance allows it to heat up efficiently. Ensure that the resistance is balanced so that the wire can reach the desired temperature without excessive energy consumption.
- Durability: In addition to resisting oxidation and other forms of thermal degradation, the wire should maintain its structural integrity over repeated heating and cooling cycles.
- Flexibility: Although flexibility is not as critical as the other properties, a degree of flexibility can be advantageous, allowing the wire to be easily manipulated into different shapes or configurations.
Suitability of 316 Grade for Hot Cutting Applications
316 grade stainless steel exhibits several properties that make it a candidate for hot cutting applications, including excellent corrosion resistance, significant heat tolerance, and good mechanical strength. However, when evaluating its suitability as a hot cutting wire, several factors need consideration:
- Heat Tolerance: For all hot cutting applications, where temperatures can exceed 899°C (1650°F), 316 grade steel may not be sufficient.
- Electrical Resistance: 316 stainless steel has a lower electrical resistance than traditional hot cutting materials like nichrome. This may affect the precision and quality of the cut since it may not heat as efficiently or evenly.
- Durability and Longevity: Over time, repeated thermal cycling can affect the 316 wire’s strength, especially at high temperatures, resulting in a shorter lifespan than materials designed specifically for high temperatures.
Comparison with Traditional Hot Cutting Wires
In the past, materials like nichrome (an alloy of nickel and chromium) and kanthal (an alloy of iron, chromium, and aluminum) have been used for hot cutting wires due to their optimal balance of heat tolerance, electrical resistance, and durability. In comparison to these materials, 316 stainless steel:
- Performs at Lower Temperatures: Compared to nichrome or kanthal, its higher temperature capability limits its use to applications requiring lower cutting temperatures.
- Has Lower Electrical Resistance: To achieve similar temperatures, it may require higher power inputs due to its less efficient conversion of electrical energy into heat.
- May Offer Cost Advantages: Due to its widespread availability and lower price point, 316 stainless steel might be more cost-effective depending on the application.
The lower heat tolerance and electrical resistance of 316 grade stainless steel limit its suitability as a hot cutting wire. There is a balance between performance and cost with 316, which makes it a viable option for applications where these limitations are not prohibitive.
Case Studies
While specific case studies of 316 grade stainless steel wire used in high-temperature cutting are scarce due to its niche application, theoretical applications can highlight its potential. For instance, in a controlled environment where temperature requirements are below the threshold of 316 stainless steel’s heat tolerance, such as cutting through synthetic fabrics or thin plastics, 316 wire could theoretically serve as an efficient cutting tool. The wire’s inherent corrosion resistance and strength at moderate temperatures might also make it suitable for applications in humid or corrosive environments where other hot cutting wires would degrade more rapidly.
Another hypothetical application could involve precision cutting in the culinary industry for designing specialised equipment. Here, the 316 grade’s food safety and resistance to tarnishing could offer added value. Although these applications are speculative, they suggest scenarios where 316 stainless steel wire’s unique properties could be leveraged effectively, provided the operational parameters align with the material’s capabilities.
A study into the suitability of 316 grade stainless steel as a hot cutting wire reveals a material with commendable properties, such as corrosion resistance and mechanical strength. High-temperature applications are limited by its lower electrical resistance and heat tolerance compared to traditional hot cutting materials. In order to ensure optimal performance and longevity, material properties must be aligned with the specific requirements of high-temperature applications.
Crazy Wire Company can assist those navigating the complexity of choosing the right wire for high-temperature applications. Taking into account your unique operational requirements, our experts can guide you through choosing the perfect wire.
You can find detailed specifications and a comprehensive selection of 316 grade wire on our website. We can help you find the best wire option for your needs, ensuring the success of your project.
We offer also a massive range of stainless steel wire and nichrome wire through our store. Choose the wire that you want to work with and we’ll get spooling.
If you’re interested in learning more about wire, check out our other blog on Everything You Need to Know About Wires.
We are also proud to supply this product on our highly popular eBay store, check us out there too.
Thank you for checking out our site.
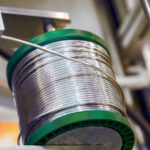
Nichrome Wire Safety: Top Tips for Working Safely
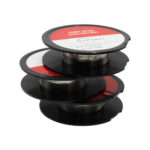
Best Wire for Electronics Projects
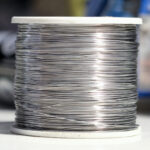
Is Ni80 Wire Suitable for DIY Heating Elements
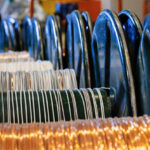
Wire Grades Explained
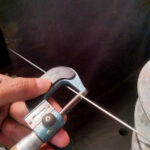
How Wire Diameter Affects Strength and Flexibility
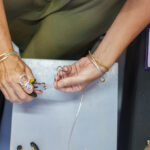
How to Cut and Shape Wire for Custom Applications
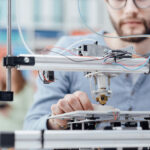
Can Wire Be Used in 3D Printing?
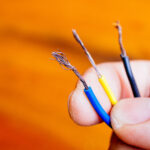
How Wire Composition Affects Conductivity
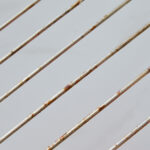