Tensioning line wires play an integral role in various structural projects, serving as the backbone for applications that demand both strength and resilience.
Wire can have a significant impact on both the longevity and effectiveness of a project, whether it’s anchoring a vineyard trellis or securing livestock fencing. The Crazy Wire Company understands the importance of this decision and offers a comprehensive range of both galvanised and PVC-coated steel wires. We will explore the nuances of these materials in this guide, so that you can make an informed decision regarding your specific project needs.
Hopefully by the end of this article you will be able to select the best option for your project.
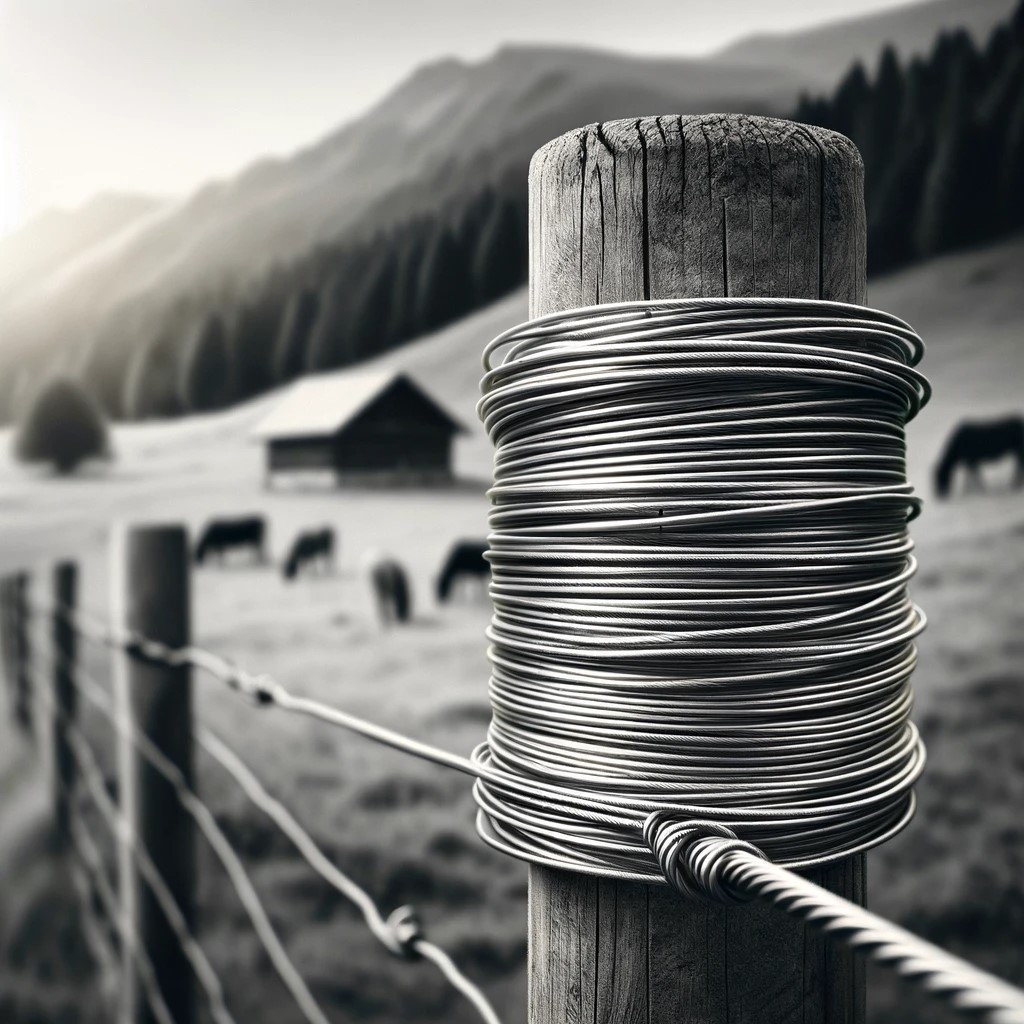
Understanding Tension Line Wires
Designed to withstand force and load, tension line wires maintain their form and position under load. Structures requiring a balance between flexibility and rigidity rely on them for the necessary give-and-take to prevent structural failures. There are many applications for these products, ranging from agricultural uses to security measures in commercial and residential buildings.
By coating steel wire with zinc, galvanisation significantly improves the wire’s durability. The zinc acts as a sacrificial anode, which means it will corrode instead of the steel, thereby extending the wire’s life. Due to their rust resistance and weather resistance, galvanised wires are a staple in outdoor and industrial settings.
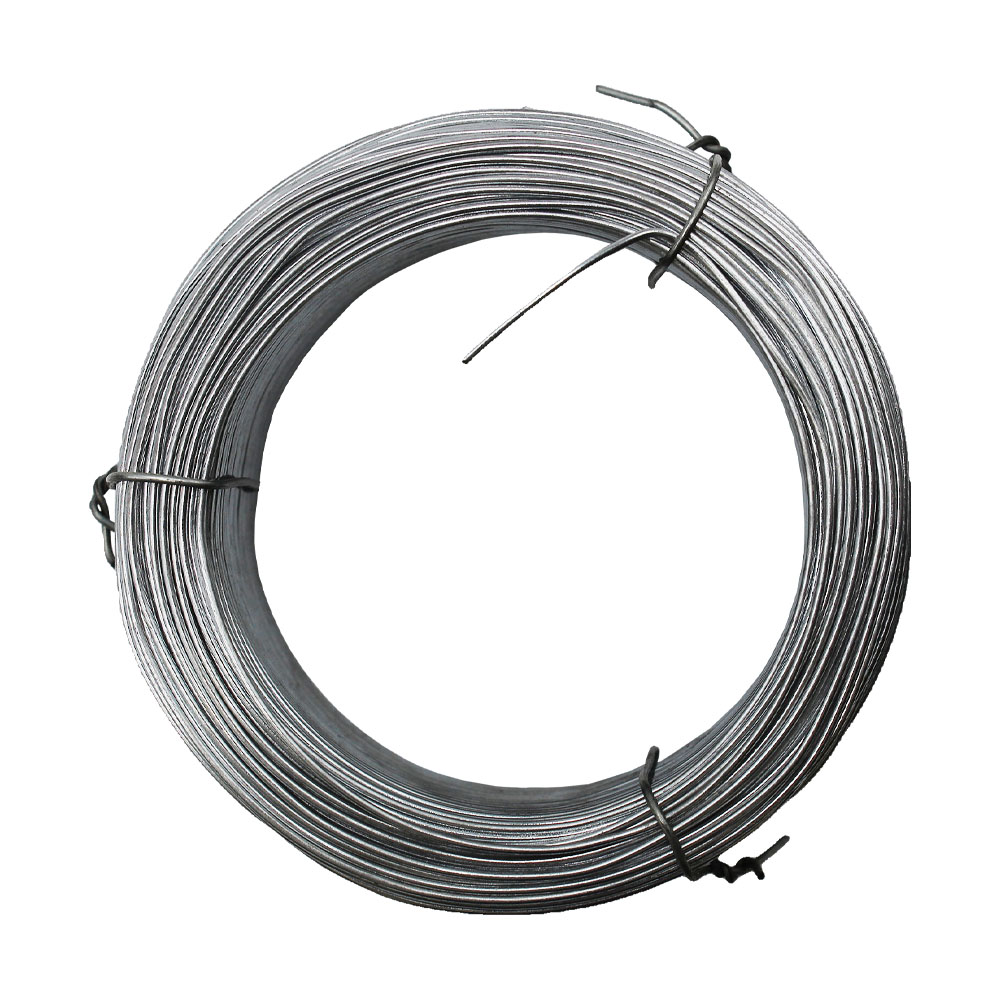
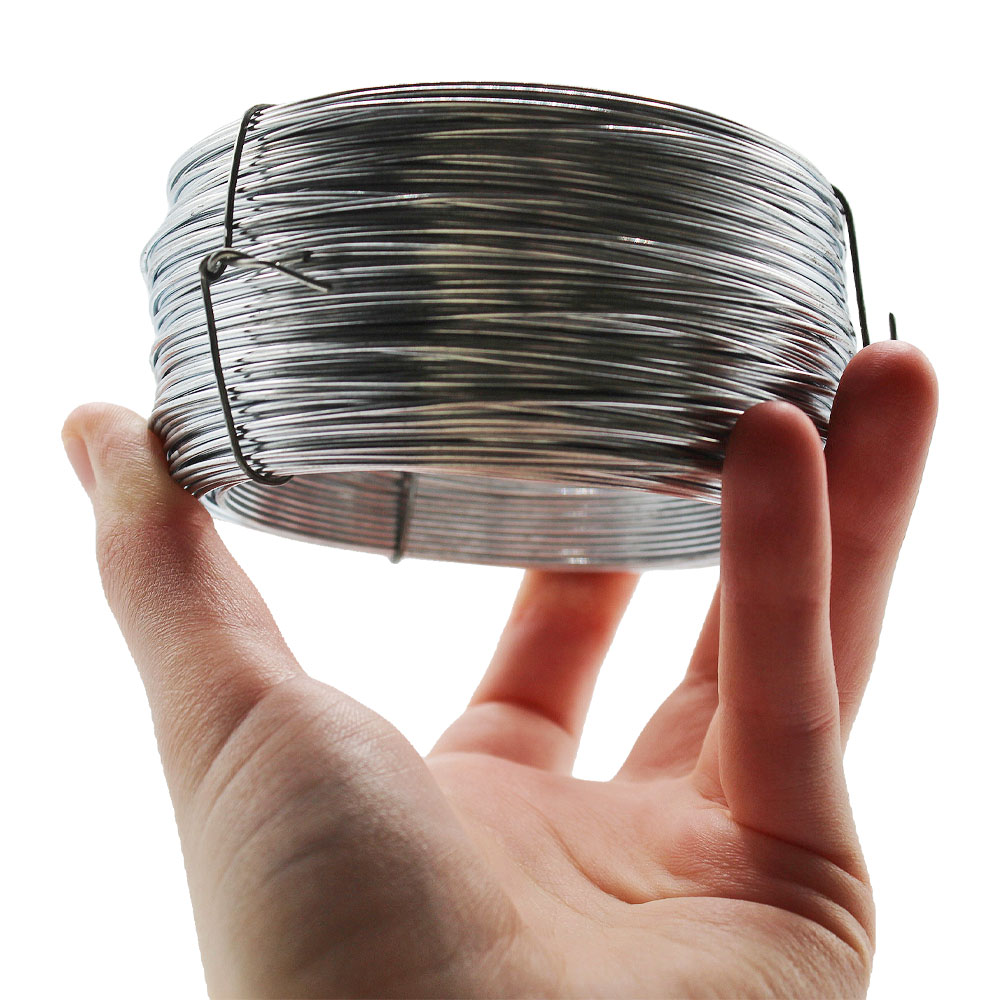
Benefits of Galvanised Steel Wires
The exceptional durability and cost-effectiveness of galvanised steel wire make it a popular choice. It’s ideal for environments exposed to moisture, varying temperatures, and physical wear. We galvanise our wires so that they can withstand these conditions without succumbing to corrosion, which could compromise their structural integrity.
Our galvanised wires range in thickness from 1mm, suitable for delicate work and lighter loads, to 3mm, designed for heavier loads. 1mm wire is often used in domestic settings, such as garden fencing or DIY projects, where flexibility is just as important as strength. The 1.25mm to 3mm wires provide robust solutions for agricultural fencing, supporting climbing plants in vineyards, or serving as tension wires in construction settings where its ability to maintain tension without elongation is essential.
No matter what your project demands-elasticity, tensile strength, or longevity-there’s a galvanised wire to meet it.
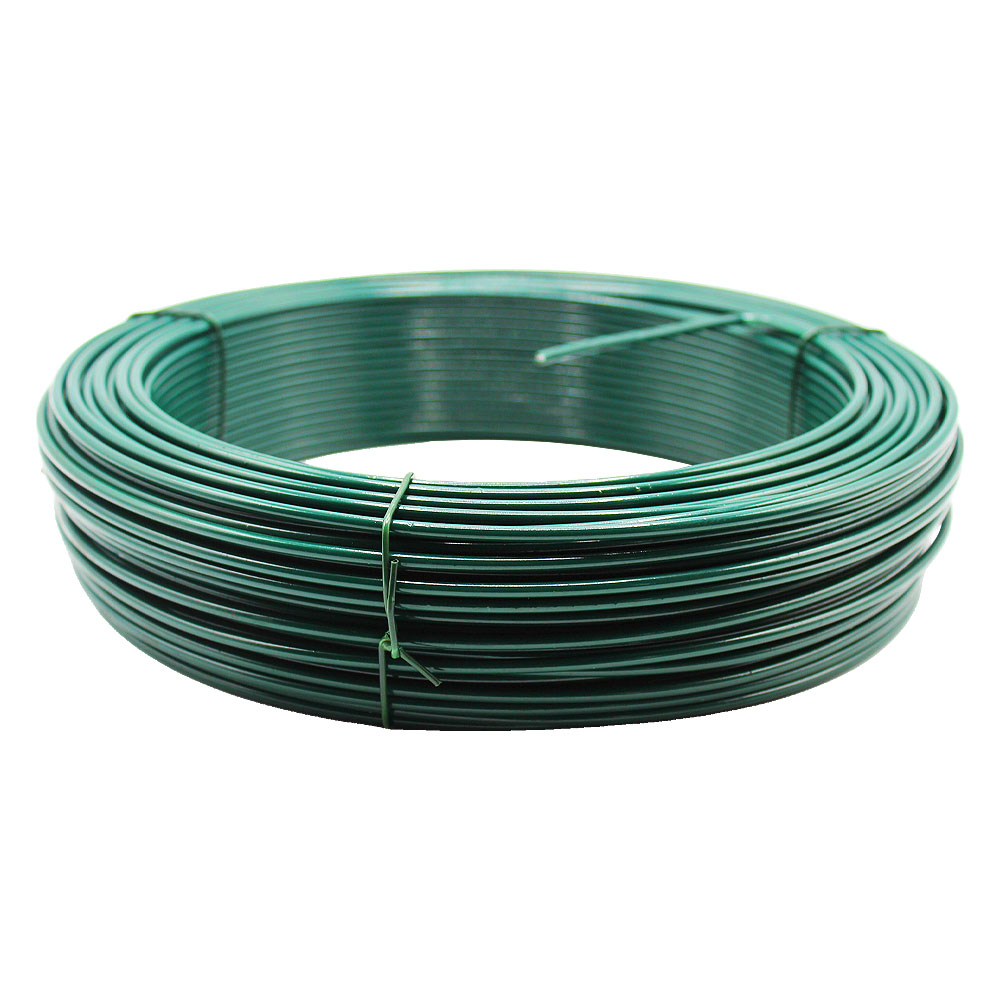
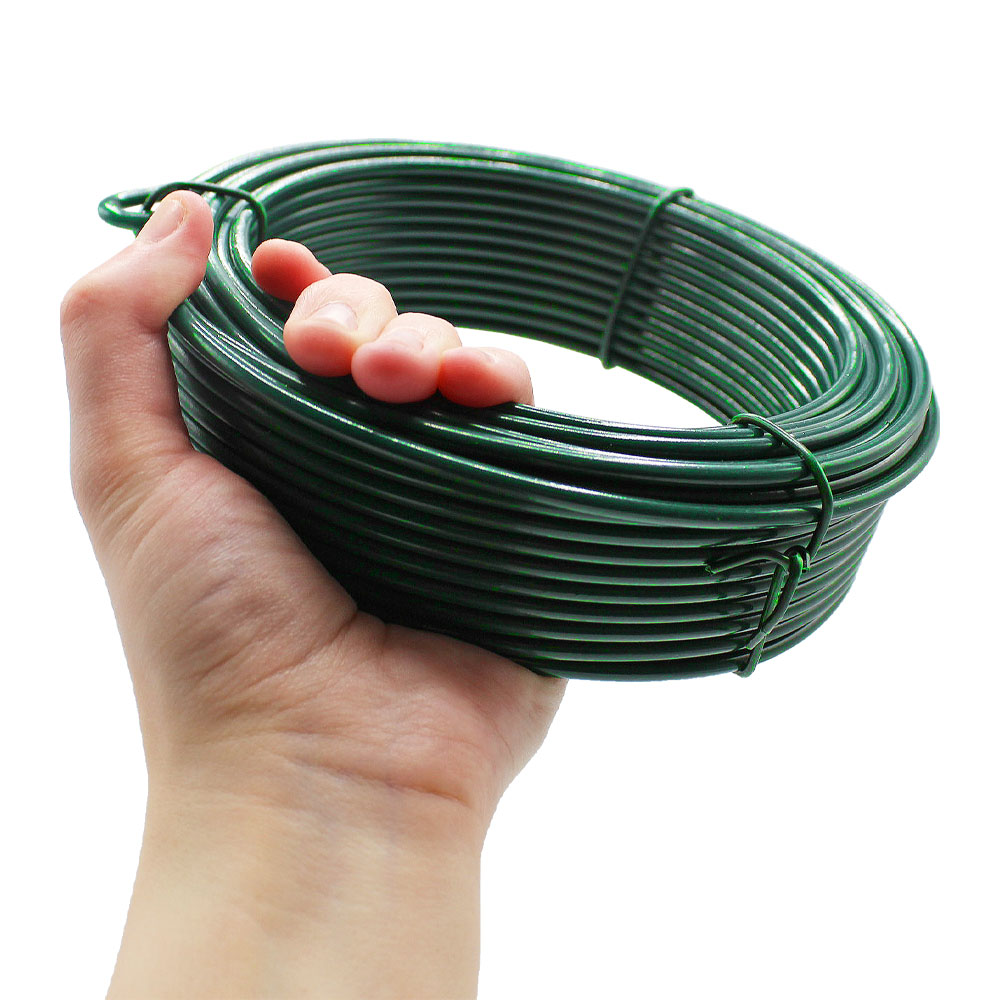
Advantages of PVC-Coated Tension Line Wires
PVC-coated tension line wires offer additional protection and versatility over plain galvanised wires. PVC (polyvinyl chloride) coating protects wire from wear and corrosion caused by environmental factors. In environments with high levels of corrosion, such as coastal areas with high levels of salt spray or industrial settings with high levels of chemical exposure, this protective layer is especially beneficial.
PVC coatings also provide a degree of cushioning and a smoother surface when in contact with other materials, making them less abrasive. By providing a softer barrier, the coating is particularly advantageous in applications like animal fencing. Additionally, the green colour of the PVC coating blends seamlessly with outdoor environments, making it an aesthetically pleasing option for residential and park fencing.
The green PVC-coated wire is also highly visible, which is an important safety feature in applications such as ski slopes or construction safety barriers. Compared to bare wires, the coating allows for easier handling and installation since it can be more pliable and less likely to cause cuts.
Comparative Analysis: Galvanised vs. PVC-Coated
There are several factors to consider when choosing between galvanised and PVC-coated tension line wires. Both wires offer robust corrosion resistance, but the PVC coating offers an advantage in particularly harsh environments and can significantly extend the wire’s life.
Another important factor is durability. It is worth noting that galvanised wire is sturdy, but the additional layer of PVC on coated wires can protect it from scratches and impacts that could compromise its galvanisation. In applications where physical wear is common, PVC-coated wires may last longer.
In terms of cost, galvanised wire is typically more economical upfront. PVC-coated wire may offer better value over time, however, considering its potential longevity and reduced maintenance.
Depending on the project, the green PVC-coated wire can blend with or stand out in its environment, depending on its aesthetics.
Ultimately, the choice between galvanised and PVC-coated wires should be based on the application demands, the environment in which the wire will be used, and the long-term maintenance requirements. Various industries use both types of wire, and the right choice will ensure your project’s success and durability.
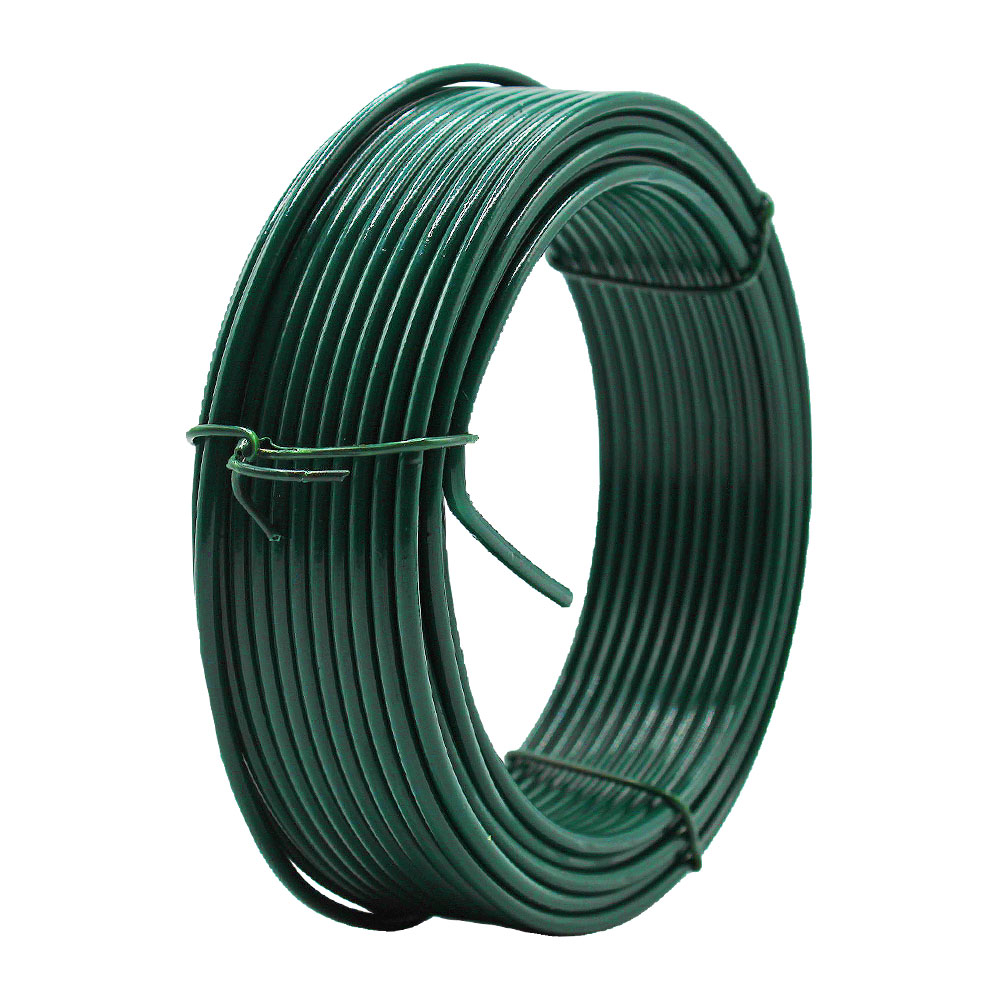
Selecting the Right Wire Thickness
Choosing the correct wire thickness is a pivotal decision that can determine the success of your project. The thickness of the wire, often measured in millimeters, directly influences its tensile strength, flexibility, and weight-bearing capacity. Here are some guidelines to help you select the right wire thickness:
Assess the Load: Determine how much weight or force the wire must support. In order to increase tensile strength, thicker wires are required for heavier loads.
Consider the Flexibility Needs: Choose a thinner wire that will provide the necessary flexibility without fracturing if the wire must be bent or twisted.
Understand the Environmental Conditions: Consider factors such as wind, weather, and potential impacts when designing outdoor applications. These conditions may be better handled by thicker wires.
Balance with Budget: Wires with a thicker diameter are generally more expensive. Making a cost-effective choice requires balancing material costs with performance requirements.
Consult Industry Standards: For guidance on recommended wire thickness for specific applications, consult industry standards.
A vineyard may use a 1mm thick wire for trellising to support vines while maintaining flexibility. Security fences, on the other hand, may require a wire that is 2mm thick or greater in order to withstand attempts to cut or break them.
Installation Tips for Tension Line Wires
Proper installation of tension line wires, whether galvanised or PVC-coated, is key to their performance and longevity. Here are some best practices:
Use the Right Tools: Make sure you have the right tools for cutting and tensioning the wire. This could include wire cutters, tensioning devices, and safety equipment.
Avoid Sharp Bends: Avoid sharp bends in the wire when installing, as these can cause weak points. Where bends are necessary, use a smooth, gradual curve.
Maintain Even Tension: Avoid sagging or overstressing any single point by applying tension evenly across the wire. For the wire to function properly, this is crucial.
Check the Connections: Make sure all connections and terminations are secure. Use galvanised fittings to prevent corrosion on galvanised wire, and do not compromise the coating on PVC-coated wire.
Regular Inspections: As soon as the wire is installed, it is important to check regularly for signs of wear and corrosion, and if necessary, re-tension the wire.
By following these guidelines, you’ll ensure that the wire is not only installed correctly but also set up for a long, useful life in its application.
Maintenance and Longevity
Both galvanised and PVC-coated tension line wires require regular maintenance to ensure long-term reliability. Check galvanised wires periodically for rust or corrosion, especially at the cut ends where the protective zinc coating may have been removed. These vulnerable spots can be protected by applying zinc-rich paint or spray. As well as keeping the wire free of debris and dirt that can retain moisture, you can prevent corrosion by keeping it clean.
Despite being more corrosion-resistant, PVC-coated wires should be checked for cracks or splits in the coating. When the wire’s underlying steel is exposed, it can rust, compromising its strength. A PVC adhesive can prevent further deterioration of a damaged coating if it is sealed.
Friction wears both types of wire, especially where they contact other materials. By lubricating these contact points regularly, friction can be reduced and the wire’s life can be extended. Wires will also remain structurally sound over time if they are not over-tensioned during installation.
It is important to consider the environment, the load, and the aesthetic preference when choosing between galvanised and PVC-coated tension line wires. The success and longevity of your project can be assured by understanding the unique properties and maintenance needs of each wire type.
You can get personalised advice and explore a full selection of tension line wires at The Crazy Wire Company. Make an informed purchase with our expert guidance by visiting our website to find the perfect wire for your project.
Make sure your project’s foundation is as strong and enduring as our service.
We offer also a massive range of stainless steel wire and nichrome wire through our store. Choose the wire that you want to work with and we’ll get spooling.
If you’re interested in learning more about wire, check out our other blog on Everything You Need to Know About Wires.
We are also proud to supply this product on our highly popular eBay store, check us out there too.
Thank you for checking out our site.
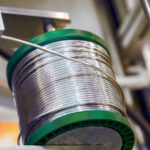
Nichrome Wire Safety: Top Tips for Working Safely
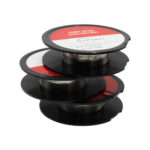
Best Wire for Electronics Projects
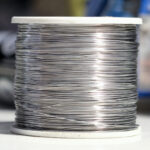
Is Ni80 Wire Suitable for DIY Heating Elements
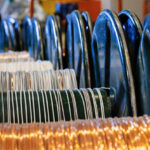
Wire Grades Explained
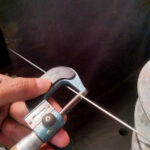
How Wire Diameter Affects Strength and Flexibility
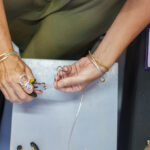
How to Cut and Shape Wire for Custom Applications
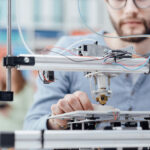
Can Wire Be Used in 3D Printing?
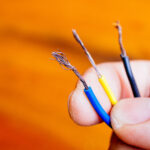
How Wire Composition Affects Conductivity
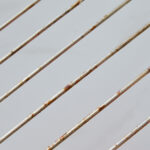