Safety wire is an essential component in many industries, providing a reliable method of securing fasteners and preventing accidental loosening due to vibration and other forces. A variety of industries rely on this versatile tool, including aviation, motorsports, and manufacturing. You’ll learn about the different types of safety wire, how they work, and how to select the best type for your needs in this comprehensive guide. We’ll explore why safety wires are such an important component of ensuring safety and reliability by looking at it in detail.
What is Safety Wire?
Safety wire, also known as lock wire, is a type of wire used to secure bolts, nuts, and other fasteners to prevent them from coming loose. It’s typically made from stainless steel or other durable materials and is twisted to create a secure connection. The wire is often used in conjunction with drilled fasteners, which allow the wire to be threaded through and twisted into place. The primary goal of safe wire is to provide a secondary locking mechanism that ensures fasteners remain secure under various conditions, including vibration, thermal expansion, and mechanical stress.
Types of Safety Wire
Safety wire comes in several different types, each suited for specific applications. Understanding the differences between these types can help you choose the right wire for your project.
Stainless Steel Safety Wire
Description: Stainless steel safety wire is the most common type, known for its high strength, corrosion resistance, and durability. It’s available in various diameters, typically ranging from 0.015 inches to 0.041 inches.
Uses:
- Aviation: Used extensively to secure fasteners in aircraft engines and other critical components.
- Motorsports: Ensures the reliability of fasteners in high-vibration environments.
- Marine Applications: Resists corrosion in saltwater environments, making it ideal for securing hardware on boats and ships.
Advantages:
- High tensile strength.
- Excellent corrosion resistance.
- Durable under extreme conditions.
Monel Safety Wire
Description: Monel safe wire is made from a nickel-copper alloy, offering superior corrosion resistance, especially in harsh environments such as saltwater and chemical exposure.
Uses:
- Marine and Offshore Applications: Ideal for use in environments with high exposure to saltwater.
- Chemical Plants: Resists corrosion from various chemicals and gases.
- Aerospace: Used in high-stress applications where corrosion resistance is critical.
Advantages:
- Outstanding corrosion resistance.
- Suitable for harsh environments.
- Maintains strength and durability in extreme conditions.
Inconel Safety Wire
Description: Inconel safe wire is made from a nickel-chromium alloy, known for its excellent resistance to oxidation and high-temperature stability. It’s often used in environments where both high strength and temperature resistance are required.
Uses:
- Aerospace: Ideal for securing fasteners in high-temperature areas, such as jet engines.
- Nuclear Power Plants: Used in applications where radiation and high temperatures are present.
- Chemical Processing Plants: Resists corrosion from aggressive chemicals and high temperatures.
Advantages:
- High-temperature resistance.
- Excellent oxidation resistance.
- Strong and durable in extreme conditions.
Titanium Safety Wire
Description: Titanium safe wire is lightweight yet strong, with excellent corrosion resistance and a high strength-to-weight ratio. It’s often used in applications where weight reduction is crucial without compromising strength.
Uses:
- Aerospace: Reduces weight while maintaining strength and durability.
- Motorsports: Provides a lightweight solution for securing fasteners in high-performance vehicles.
- Medical Devices: Used in applications where biocompatibility and strength are required.
Advantages:
- Lightweight and strong.
- Excellent corrosion resistance.
- High strength-to-weight ratio.
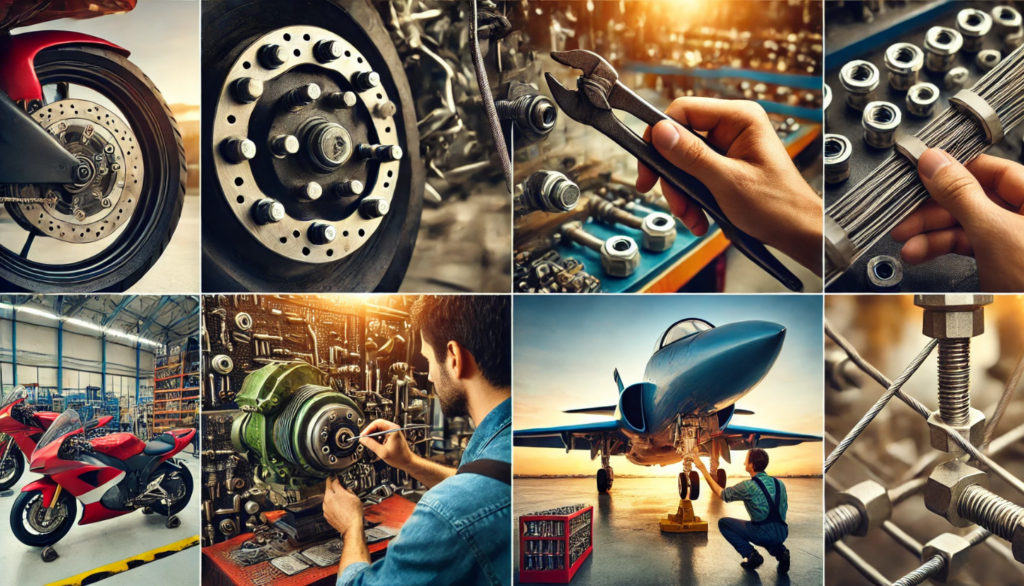
Selecting the Right Safety Wire
Choosing the right safety wire depends on several factors, including the specific application, environmental conditions, and required strength. Here are some key considerations to help you make the best choice:
Application Requirements
Consider the specific requirements of your application. For example, in the aerospace industry, where high temperatures and vibration are common, a wire with high-temperature resistance and durability, such as Inconel or stainless steel, may be required. In contrast, marine applications benefit from Monel’s superior corrosion resistance.
Environmental Conditions
The environment where the safety wire will be used is a critical factor. Stainless steel is a versatile choice for many environments, but in highly corrosive conditions, such as saltwater or chemical exposure, Monel or Inconel may be more suitable. Titanium is an excellent choice for applications requiring both corrosion resistance and weight reduction.
Diameter and Strength
Safety wire is available in various diameters, with thicker wires providing greater strength. The diameter needed depends on the size of the fasteners and the level of security required. For example, a 0.020-inch wire may be sufficient for small fasteners in low-vibration environments, while a 0.041-inch wire may be needed for larger fasteners subjected to high stress and vibration.
Ease of Use
Consider the ease of use when selecting safe wire. Some materials, like stainless steel, are easier to work with and manipulate, making the installation process smoother. Titanium, while strong and lightweight, may be more challenging to work with due to its toughness.
How to Use Safety Wire
Using safety wire effectively requires proper tools and techniques to ensure a secure and reliable installation. Here’s a step-by-step guide to using safe wire:
Tools Needed
- Safety wire pliers
- Wire cutters
- Safety wire
Steps to Install Safety Wire
Preparation:
- Select the appropriate diameter and type of safe wire for your application.
- Ensure that the fasteners have pre-drilled holes for threading the wire.
Threading the Wire:
- Cut a length of wire sufficient to secure the fasteners.
- Thread the wire through the drilled holes in the fastener. If securing multiple fasteners, ensure the wire is threaded through each one in succession.
Twisting the Wire:
- Use safety wire pliers to twist the wire. Grip the ends of the wire with the pliers and twist them together. Ensure that the twists are tight and even, typically around 6-8 twists per inch.
Securing the Ends:
- After twisting the wire, cut off any excess, leaving about 1/2 inch of wire.
- Bend the ends of the wire back towards the fastener to prevent them from snagging or causing injury.
Inspection:
- Inspect the installation to ensure the wire is tight and secure. There should be no slack in the wire, and the twists should be uniform and tight.
Safety Wire Applications
Safety wire is used in a variety of applications across different industries. Here are some common uses:
Aviation
In the aviation industry, safe wire is critical for securing fasteners in aircraft engines, landing gear, and other essential components. The constant vibration and stress experienced during flight necessitate the use of safety wire to prevent catastrophic failures.
Motorsports
Motorsports involve high speeds and intense vibrations, making safe wire an essential component for securing fasteners on race cars and motorcycles. It’s used to secure components like brake calipers, suspension parts, and engine fasteners, ensuring they remain tight during races.
Marine
In marine applications, safety wire is used to secure fasteners on boats and ships, particularly in areas exposed to saltwater. The corrosion resistance of materials like Monel and stainless steel makes them ideal for these environments.
Industrial and Manufacturing
Safety wire is also used in industrial and manufacturing settings to secure fasteners on machinery and equipment. It provides an additional layer of security, preventing bolts and nuts from loosening due to vibration and mechanical stress.
Medical Devices
In the medical field, safety wire is used in the manufacture and assembly of medical devices. Titanium safe wire, in particular, is favored for its biocompatibility and strength, ensuring the reliability of implants and surgical instruments.
Safety wire is a versatile and indispensable tool in various industries, offering a reliable method of securing fasteners and preventing them from coming loose. No matter what industry you work in, understanding safety wires and their specific uses will help you choose the best wire.
From stainless steel and Monel’s high strength and corrosion resistance to Inconel’s high-temperature stability and titanium’s lightweight durability, each type of safe wire offers unique benefits. It is important to consider the application requirements, the environment, and the required strength when selecting fasteners for your upcoming project.
Using safety wire effectively requires the right tools and techniques to ensure a tight, secure installation. Your equipment, machinery, and vehicles can be made safer and more reliable with the right safety wire, providing peace of mind and preventing costly failures.
It is a small, but crucial step to ensure the safety and integrity of your projects by incorporating safe wire. The importance of meticulous attention to detail cannot be overstated when it comes to securing aircraft components, race car parts, marine hardware, industrial machinery, or medical devices.
Thank you for taking the time to read our blog. We hope that the information above helped you in the search for the right product for your project.
If you are interesting in learning more about wires, check out our blog on Choosing the Best Tension Line for Your Project or take a look at our range of Stainless Steel Wires.
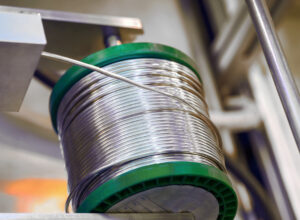
Nichrome Wire Safety: Top Tips for Working Safely
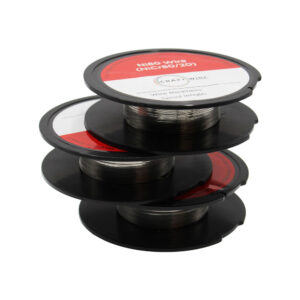
Best Wire for Electronics Projects
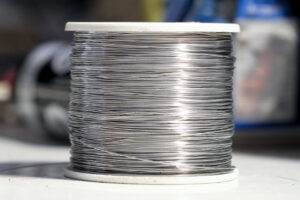
Is Ni80 Wire Suitable for DIY Heating Elements
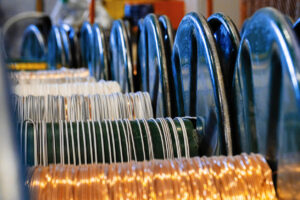
Wire Grades Explained
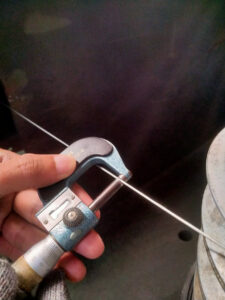
How Wire Diameter Affects Strength and Flexibility
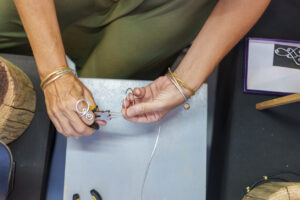
How to Cut and Shape Wire for Custom Applications
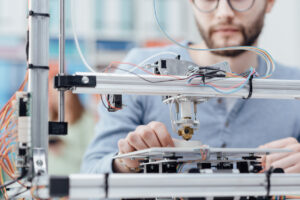
Can Wire Be Used in 3D Printing?
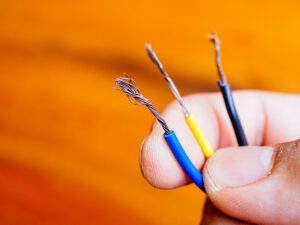
How Wire Composition Affects Conductivity
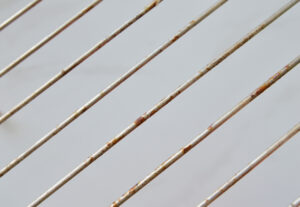