When selecting wires for outdoor applications, it’s essential to understand the differences and benefits of galvanised versus coated wires. Both types of wiring offer distinct advantages in durability, cost-effectiveness, and suitability for various environmental conditions. In this comprehensive guide, we’ll explore the nuances of galvanised vs coated wires, helping you determine the best option for your specific needs.
Understanding Galvanised vs Coated Wires
What are Galvanised Wires?
Galvanised wires are made of steel or iron that is coated with a thin layer of zinc. This process, known as galvanization, involves dipping the base metal into a molten zinc bath. The zinc coating provides a robust layer of protection against corrosion, which is especially beneficial in outdoor or moist environments.
What are Coated Wires?
Coated wires, on the other hand, generally refer to wires covered with a non-metallic coating, typically made of materials like PVC (polyvinyl chloride) or PE (polyethylene). This type of wire is designed to offer enhanced protection against various environmental factors, including UV rays, chemicals, and physical abrasion, in addition to its anti-corrosive properties.
Comparative Analysis: Galvanised vs Coated Wires
Corrosion Resistance
Galvanised Wires: The zinc coating on galvanised wires provides excellent protection against rust and corrosion. When exposed to moisture, zinc reacts to form a protective barrier of zinc carbonate, which further enhances its resistance to rust. This makes galvanised wires particularly suitable for humid, coastal, or rainy environments.
Coated Wires: While coated wires also offer good corrosion resistance, the level of protection largely depends on the type and thickness of the coating. PVC and PE coatings can effectively seal the wire from moisture and other corrosive elements. However, if the coating is breached from a cut or abrasion, the underlying metal can be exposed to corrosion.
Durability and Lifespan
Galvanised Wires: The durability of galvanised wires is generally very high, especially in environments where the zinc coating remains intact. Over time, however, the zinc can gradually erode, which might require re-coating or replacement to maintain optimal performance.
Coated Wires: The additional layer of plastic or rubber in coated wires not only prevents corrosion but also adds an extra layer of protection against mechanical damage. This can significantly extend the lifespan of the wire, especially in environments where physical impact or abrasion is a concern.
Flexibility and Ease of Use
Galvanised Wires: Galvanised wires tend to be less flexible compared to coated wires, due to the nature of the zinc coating. This might make installation slightly more challenging, especially in applications requiring the wire to bend around corners or tight spaces.
Coated Wires: The plastic or rubber coating on these wires provides enhanced flexibility, which can be a significant advantage during installation. Additionally, the smooth coating can make handling and working with these wires safer and more comfortable.
Aesthetic and Design Considerations
Galvanised Wires: Galvanised wires generally have a bright, metallic finish that can become duller over time as the zinc oxidizes. For projects where aesthetics are a priority, additional painting or treatments might be necessary.
Coated Wires: One of the advantages of coated wires is the availability of various colors, which can be chosen to blend in or contrast with the surrounding environment. This makes them particularly appealing for decorative or visible installations.
Cost Comparison
Galvanised Wires: Typically, galvanised wires are more cost-effective in the short term compared to coated wires. This makes them an attractive option for large-scale projects or applications where budget constraints are significant.
Coated Wires: While initially more expensive, the added durability and reduced maintenance needs of coated wires can lead to lower overall costs in the long term. This is particularly true in harsh environments where the risk of damage or corrosion is higher.
Environmental Considerations
Galvanised Wires: The galvanisation process involves the use of zinc, which is a natural element and generally less harmful to the environment compared to some plastics used in wire coatings.
Coated Wires: The environmental impact of coated wires can vary depending on the type of plastic used. PVC, for example, can release harmful chemicals if burned and is not biodegradable. More eco-friendly coatings are available, but they may come at a higher cost.
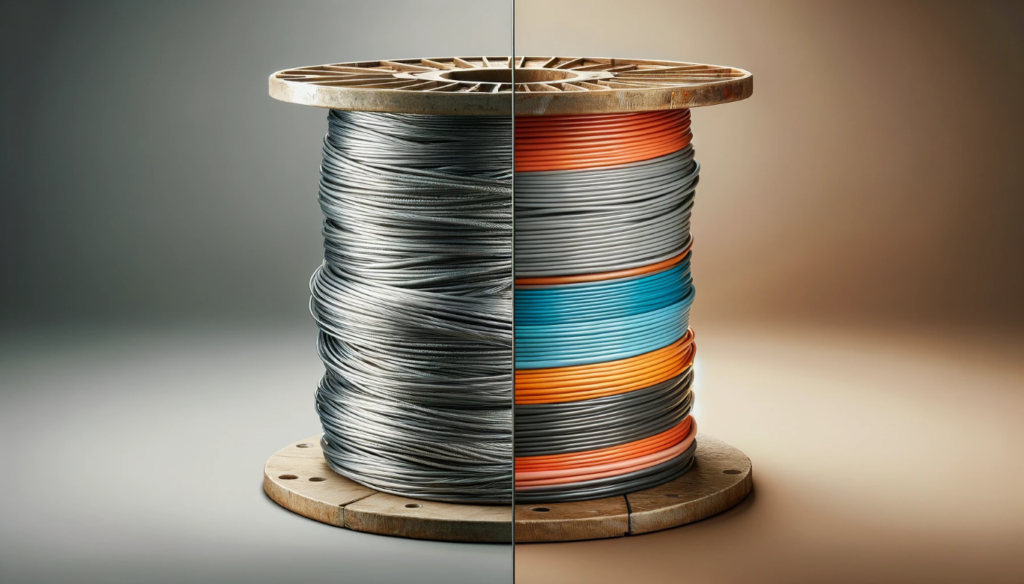
Pros and Cons: Galvanised vs Coated Wires
Here’s a table summarising the pros and cons of galvanised wires and other coated wires, which will help illustrate their suitability for different outdoor applications:
Feature | Galvanised Wires | Coated Wires |
---|---|---|
Corrosion Resistance | High due to zinc coating | Varies; generally good with proper coating |
Durability | Good, but can degrade if zinc wears off | Excellent, enhanced by protective coating |
Flexibility | Less flexible | More flexible |
Installation Ease | Moderately easy to handle | Easier to handle due to flexibility |
Aesthetic Variety | Limited, typically metallic | Available in various colors |
Cost | Generally lower initial cost | Higher initial cost, but may be economical in the long run |
Environmental Impact | Zinc is less harmful than some coatings | Depends on coating type; PVC can be harmful |
Long-term Maintenance | May require re-coating | Lower maintenance due to durable coating |
Suitability | Industrial, agricultural, utilities | Decorative, residential, areas needing color coordination |
Lifespan | Long if maintained properly | Generally longer lifespan without need for re-coating |
In conclusion, when it comes to choosing between galvanised vs coated wires for outdoor applications, both options offer unique advantages that cater to different needs and environments. Galvanised wires are excellent for projects where corrosion resistance and cost-effectiveness are paramount, making them ideal for industrial and utility applications. Coated wires, though more expensive, provide enhanced flexibility, aesthetic variety, and superior durability, which are crucial for installations requiring a blend of strength, visual appeal, and resistance to physical wear.
Ultimately, the decision should be guided by a thorough analysis of the specific conditions and demands of your project. Consider environmental factors, budget constraints, aesthetic requirements, and long-term maintenance needs when selecting your wiring solution. By doing so, you ensure that your choice not only meets the immediate requirements of your project but also contributes to its longevity and efficiency, maximizing your investment in the long run. Whether you opt for the rugged simplicity of galvanised wires or the versatile protection of coated wires, understanding their distinct properties will help you make the best choice for enduring success in any outdoor setting.
We offer also a massive range of stainless steel wire and nichrome wire through our store. Choose the wire that you want to work with and we’ll get spooling.
If you’re interested in learning more about wire, check out our other blog on Everything You Need to Know About Wires.
We are also proud to supply this product on our highly popular eBay store, check us out there too.
Thank you for checking out our site.
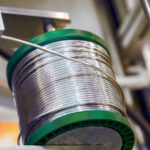
Nichrome Wire Safety: Top Tips for Working Safely
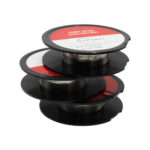
Best Wire for Electronics Projects
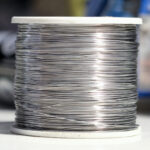
Is Ni80 Wire Suitable for DIY Heating Elements
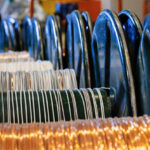
Wire Grades Explained
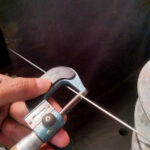
How Wire Diameter Affects Strength and Flexibility
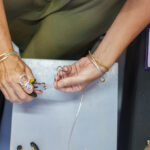
How to Cut and Shape Wire for Custom Applications
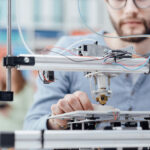
Can Wire Be Used in 3D Printing?
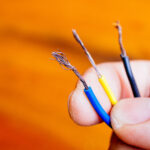
How Wire Composition Affects Conductivity
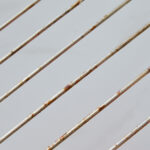