In the world of mechanical engineering and aerospace industries, where precision and safety are paramount, the term “lockwire” holds significant importance. Known also as safety wire or safety lock wire, this key component ensures the integrity of critical systems by securing fasteners and preventing unintended loosening. We explore the applications, types, and techniques of lockwire, as well as why it remains indispensable across various industries in this comprehensive guide.
What is Lockwire?
Lockwire is a type of wire used to secure bolts, nuts, screws, and other fasteners in place to prevent them from loosening due to vibration or other forces. It typically involves twisting the wire around the fastener and securing it with specific techniques to ensure a tight and reliable hold. This method is essential in industries where even the smallest mechanical failure can lead to catastrophic consequences, such as aviation, automotive, and manufacturing sectors.
Applications of Lockwire
1. Aerospace Industry: In aviation and aerospace, where safety is non-negotiable, lockwire is extensively used to secure critical components such as bolts and fittings in aircraft engines, landing gear, and control systems.
2. Automotive Sector: Lockwire finds applications in racing cars, motorcycles, and high-performance vehicles where components experience extreme vibrations and stresses. This necessitates secure fastening to maintain operational safety.
3. Manufacturing and Machinery: Various machinery and equipment in manufacturing plants rely on lockwire to ensure that bolts and fasteners do not come loose during operation. This prevents downtime and ensuring operational efficiency.
Types of Lockwire
Lockwire comes in different materials and configurations to suit specific application requirements:
1. Material Types:
- Stainless Steel: Known for its corrosion resistance and strength, stainless steel lockwire is commonly used in aerospace and marine applications.
- Inconel: Provides superior resistance to high temperatures and corrosion, making it suitable for applications in extreme environments.
- Monel: Offers excellent resistance to corrosion, acids, and alkaline solutions, making it ideal for use in chemical and marine industries.
2. Configuration Types:
- Single Strand: Consists of a single wire typically made from stainless steel or another alloy, used for general-purpose locking.
- Twisted or Braided: Multiple strands twisted or braided together. This offers increased strength and flexibility, suitable for more demanding applications.
Techniques for Lockwiring
Achieving effective lockwiring requires precision and adherence to specific techniques:
1. Double Twisting Method: Involves wrapping the wire around the fastener and twisting it with pliers to ensure a tight and secure hold.
2. Single Twisting Method: Similar to the double twisting method but involves a single twist of the wire around the fastener.
3. Pigtail Method: Creates a loop at the end of the wire, which is twisted tightly around the fastener and then secured by bending the loop back.
Importance of Lockwire in Safety and Compliance
Lockwire isn’t just a matter of preference; it’s often a requirement dictated by safety standards and regulations in various industries:
1. Regulatory Compliance: Regulatory bodies such as the Federal Aviation Administration (FAA) mandate the use of lockwire in aircraft maintenance and manufacturing to ensure safety and compliance with aviation standards.
2. Preventive Maintenance: Lockwiring is part of routine maintenance procedures in industries where mechanical failures can have severe consequences, helping prevent accidents and equipment failures.
Advantages of Lock Wire
Prevents Loosening: The primary purpose of lockwire is to prevent bolts, nuts, screws, and other fasteners from loosening due to vibration, thermal expansion, or other mechanical forces. This helps maintain the integrity and stability of mechanical assemblies, ensuring they remain securely fastened over time.
Enhances Safety: In industries such as aerospace, automotive, and manufacturing, where even minor fastener failures can lead to catastrophic consequences, lockwire provides an additional layer of safety. By securing critical components, it reduces the risk of accidents, equipment damage, and operational downtime.
Compliance with Standards: Many regulatory bodies and standards organisations, such as the FAA (Federal Aviation Administration), require the use of lockwire in specific applications to meet safety and compliance standards. Adhering to these regulations ensures that mechanical systems are installed and maintained according to industry best practices.
Versatility in Applications: Lockwire can be used in a wide range of applications across different industries and environments. It is suitable for securing fasteners in aerospace components, automotive engines, machinery in manufacturing plants, and even in marine and offshore structures where corrosion resistance is crucial.
Corrosion Resistance: Depending on the material used (e.g., stainless steel, Inconel, Monel), lockwire offers varying degrees of corrosion resistance. This makes it suitable for applications in harsh environments where exposure to moisture, chemicals, or high temperatures could otherwise compromise the integrity of fasteners.
Proven Reliability: Lockwire has been a trusted method of fastener securing for decades. This demonstrates its reliability and effectiveness in preventing unintended loosening. Its use is supported by extensive testing and validation in demanding industrial applications.
Cost-Effective Maintenance: While initial installation may require skilled labor and specialised tools, lockwire contributes to cost-effective maintenance by reducing the frequency of fastener inspections and replacements. This helps minimise downtime and prolongs the lifespan of mechanical equipment.
Challenges and Innovations in Lockwiring
Despite its effectiveness, lockwiring poses certain challenges:
1. Time-Consuming Process: Proper lockwiring requires meticulous attention to detail and can be time-consuming, particularly in complex assemblies with numerous fasteners.
2. Automation and Innovation: Advances in automation have led to the development of semi-automated and automated lockwiring tools, reducing labor costs and increasing efficiency in industries where large-scale lockwiring is necessary.
Lockwire, or safety wire, is not merely a fastening method; it’s a critical safety measure that ensures the reliability and integrity of mechanical systems in industries where safety is paramount. There are numerous applications for lockwire, including aerospace, automotive, and manufacturing. Mechanics and engineers responsible for maintaining mechanical assemblies’ safety and efficiency must understand the types, techniques, and regulations of lockwiring.
It is impossible to overstate the importance of lockwire, even though it may appear to be a small component in the grand scheme of mechanical engineering. Fasteners remain secure, systems operate reliably, and lockwire remains indispensable in an industry that demands higher standards of safety and efficiency.
With this comprehensive overview of lockwire, we hope to provide engineers, technicians, and enthusiasts alike with a deeper understanding of its significance and application across a variety of industries. Whether securing an aircraft wing bolt or a critical component in a manufacturing facility, lockwire helps ensure that safety and reliability always come first.
We offer also a massive range of stainless steel wire and nichrome wire through our store. Choose the wire that you want to work with and we’ll get spooling.
If you’re interested in learning more about wire, check out our other blog on Everything You Need to Know About Wires.
We are also proud to supply this product on our highly popular eBay store, check us out there too.
Thank you for checking out our site.
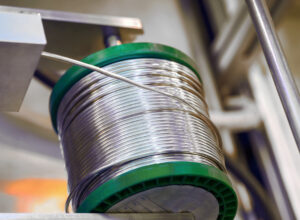
Nichrome Wire Safety: Top Tips for Working Safely
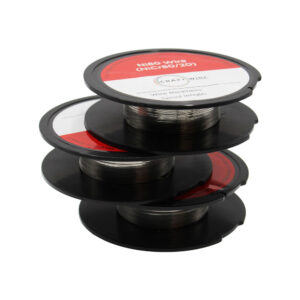
Best Wire for Electronics Projects
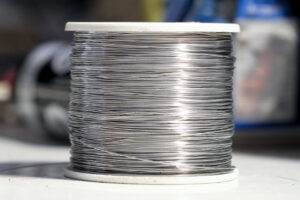
Is Ni80 Wire Suitable for DIY Heating Elements
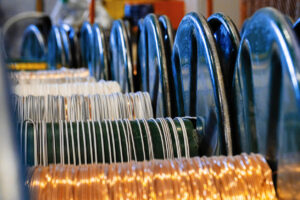
Wire Grades Explained
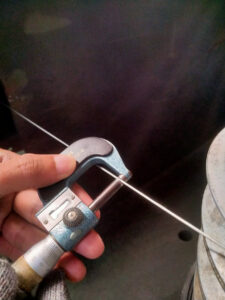
How Wire Diameter Affects Strength and Flexibility
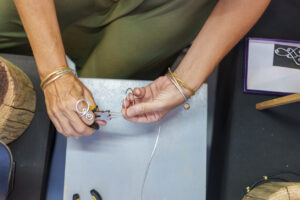
How to Cut and Shape Wire for Custom Applications
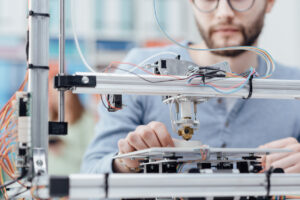
Can Wire Be Used in 3D Printing?
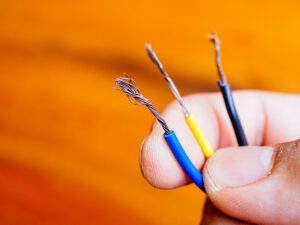
How Wire Composition Affects Conductivity
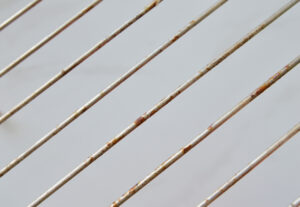