In the world of materials science and engineering, titanium wire stands out as a remarkable innovation that has revolutionised numerous industries. A material that offers unmatched performance in demanding applications due to its strength, lightweight nature, and corrosion resistance, titanium wire offers outstanding strength, lightweight, and corrosion resistance. We explore the properties of titanium steel in this blog, exploring its strength and durability, along with why it is used in so many advanced technological applications.
Understanding Titanium Wire
Titanium wire is made from titanium, a transition metal that is well-regarded for its unique combination of physical and chemical properties. The wire is typically produced by drawing titanium through a series of dies to achieve the desired diameter, which can range from ultra-thin wires used in medical implants to thicker wires used in industrial applications.
Properties of Titanium
Strength
One of the most significant properties of titanium wire is its high strength-to-weight ratio. Titanium is as strong as steel but about 45% lighter, making it an ideal material for applications where weight savings are crucial. This characteristic is particularly valuable in the aerospace, automotive, and sporting goods industries, where reducing weight without sacrificing strength can lead to improved performance and fuel efficiency.
Durability
Titanium’s durability is another key factor that makes it an attractive material. It has excellent fatigue resistance, meaning it can withstand repeated loading and unloading cycles without experiencing significant degradation. This property is essential in applications such as aircraft components, where materials are subjected to constant stress and must maintain their integrity over long periods.
Corrosion Resistance
Titanium wire is renowned for its exceptional corrosion resistance, which is superior to many other metals. This resistance is due to the formation of a stable oxide layer on the surface of the titanium when it is exposed to oxygen. This oxide layer acts as a protective barrier, preventing further oxidation and corrosion. As a result, titanium metal is highly suitable for use in harsh environments, such as marine and chemical processing applications, where other metals would quickly deteriorate.
Biocompatibility
Titanium is also biocompatible, meaning it is not harmful or toxic to living tissue. This property has led to its widespread use in the medical field, particularly in the manufacture of implants and surgical instruments. Titanium steel is used in various medical devices, including pacemaker leads, dental implants, and orthopedic implants, where its strength, durability, and compatibility with the human body are critical.
Applications of Titanium Wire
Aerospace Industry
In the aerospace industry, the demand for materials that offer high strength, low weight, and excellent durability is paramount. Titanium wire meets these requirements perfectly, making it a preferred choice for various aerospace components. It is used in the manufacture of aircraft engines, airframes, and fasteners, where its ability to withstand extreme conditions and resist corrosion is crucial. The use of titanium metal contributes to the overall performance, safety, and fuel efficiency of aircraft.
Automotive Industry
The automotive industry has also embraced titanium wire for similar reasons. High-performance vehicles, including sports cars and motorcycles, benefit from titanium wire’s strength and lightweight properties. Titanium exhaust systems, valve springs, and connecting rods are some of the components where titanium wire is utilized to enhance performance and reduce weight. The durability of titanium wire ensures that these components can withstand the high stresses and temperatures associated with automotive applications.
Medical Field
As mentioned earlier, titanium wire’s biocompatibility makes it invaluable in the medical field. Orthopedic implants, such as hip and knee replacements, often incorporate titanium wire to provide structural support and ensure long-term functionality. Additionally, titanium steel is used in dental implants, where its strength and resistance to corrosion ensure the longevity and reliability of the implants. The medical industry’s reliance on titanium wire underscores its importance in improving patient outcomes and quality of life.
Marine Applications
The marine environment is notoriously harsh, with saltwater and other corrosive elements posing significant challenges to materials. Titanium wire’s exceptional corrosion resistance makes it an ideal choice for marine applications. It is used in the construction of ship components, offshore drilling equipment, and underwater cables, where its durability ensures long-term performance and reliability. The ability of titanium steel to resist corrosion in such environments reduces maintenance costs and extends the lifespan of critical marine infrastructure.
Industrial Uses
Beyond the specialized applications in aerospace, automotive, medical, and marine industries, titanium wire also finds use in various industrial applications. Chemical processing plants, for instance, utilize titanium wire in heat exchangers, reactors, and piping systems. The chemical resistance and durability of titanium wire make it suitable for handling corrosive substances and high-temperature processes. Additionally, titanium metal is used in the manufacture of springs, fasteners, and filters, where its strength and reliability are essential.
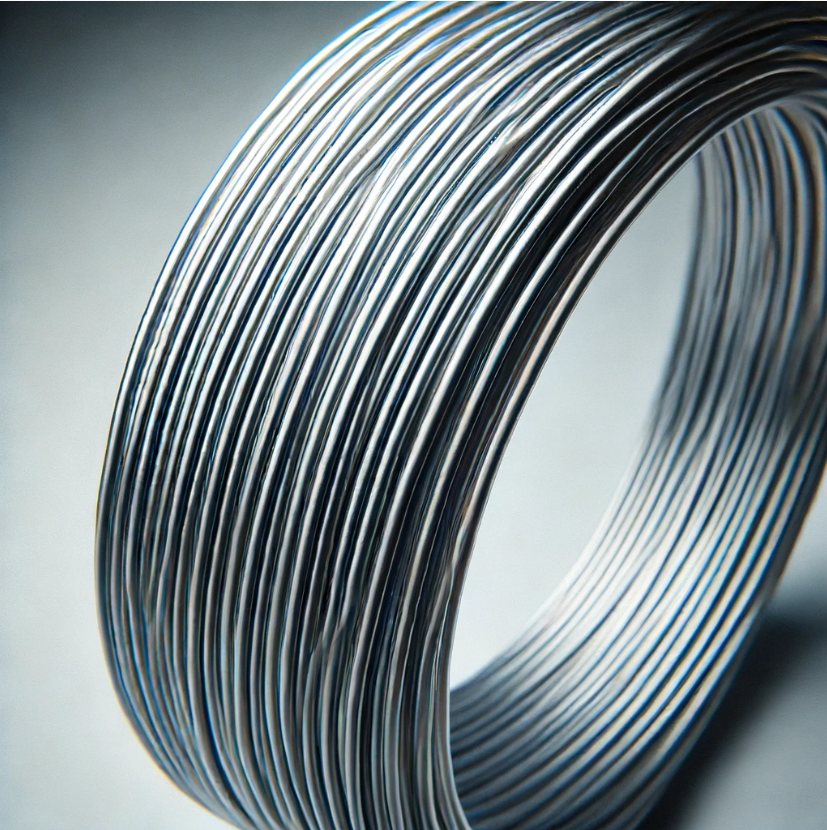
Advantages of Titanium Wire
High Strength-to-Weight Ratio
The high strength-to-weight ratio of titanium metal is one of its most significant advantages. This property allows for the design of lightweight yet robust structures, which is particularly important in industries where weight reduction is a priority. In aerospace and automotive applications, this translates to improved fuel efficiency, increased payload capacity, and enhanced overall performance.
Longevity and Low Maintenance
The durability of titanium wire means that components made from this material have a long service life. This longevity reduces the need for frequent replacements and maintenance, leading to cost savings over time. In industries such as aerospace and marine, where maintenance can be challenging and expensive, the use of titanium steel wire offers a significant advantage by minimising downtime and associated costs.
Corrosion Resistance
The ability of titanium wire to resist corrosion in various environments is another critical advantage. This property ensures that titanium wire can be used in applications exposed to harsh conditions without compromising its structural integrity. In chemical processing and marine applications, corrosion resistance is essential to maintaining the safety and functionality of equipment.
Biocompatibility
Titanium wire’s biocompatibility is a significant advantage in the medical field. Its use in implants and medical devices has revolutionised patient care by providing reliable and long-lasting solutions. The compatibility with the human body minimises the risk of rejection and complications, ensuring successful outcomes for patients.
Challenges and Considerations
While titanium wire offers numerous advantages, it is not without its challenges. One of the primary considerations is the cost of titanium. Titanium is more expensive than many other metals, which can be a limiting factor for some applications. However, the long-term benefits, such as reduced maintenance and extended lifespan, often justify the initial investment.
Another challenge is the difficulty of machining and forming titanium. Titanium has a tendency to gall and wear tools quickly, making it more challenging to work with compared to other metals. Specialised equipment and techniques are often required to handle titanium steel effectively, adding to the overall cost and complexity of manufacturing processes.
Future Prospects of Titanium Wire
The future of titanium wire looks promising, with ongoing research and development aimed at overcoming current challenges and expanding its applications. Advances in manufacturing techniques, such as additive manufacturing (3D printing), are opening new possibilities for the use of titanium wire. Additive manufacturing allows for the production of complex geometries and customised components, further enhancing the versatility of titanium wire.
In addition, efforts to reduce the cost of titanium steel production are underway. Innovations in extraction and refining processes could make titanium more affordable and accessible, broadening its use in various industries. As the demand for high-performance materials continues to grow, titanium steel wire is likely to play an increasingly important role in meeting the needs of advanced technological applications.
Titanium wire is a remarkable material that offers a unique combination of strength, durability, corrosion resistance, and biocompatibility. The versatility of this material makes it indispensable in a wide range of industries, from aerospace and automotive to medical and marine. Although titanium wire has challenges such as cost and machining difficulties, it has long-term benefits and the potential for future advancement. Strength and durability of titanium wire will undoubtedly contribute to the development of innovative solutions and advancements in a variety of fields as technology continues to evolve.
Thank you for taking the time to read our blog. We hope that the information above helped you in the search for the right product for your project.
If you are interesting in learning more about wires, check out our blog on Silver Wire or take a look at our range of Stainless Steel Wires.
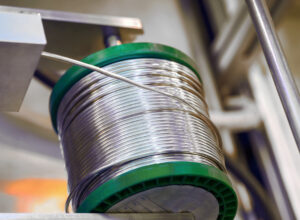
Nichrome Wire Safety: Top Tips for Working Safely
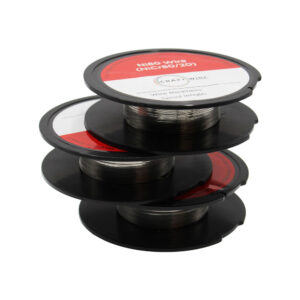
Best Wire for Electronics Projects
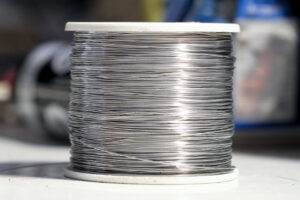
Is Ni80 Wire Suitable for DIY Heating Elements
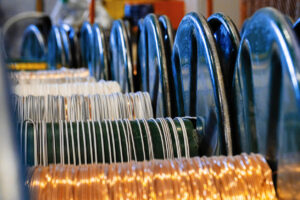
Wire Grades Explained
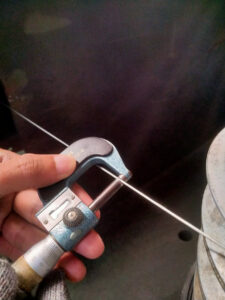
How Wire Diameter Affects Strength and Flexibility
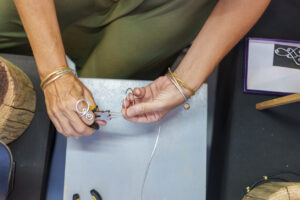
How to Cut and Shape Wire for Custom Applications
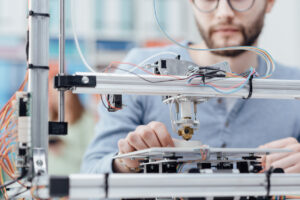
Can Wire Be Used in 3D Printing?
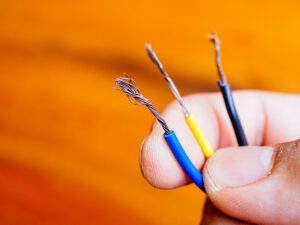
How Wire Composition Affects Conductivity
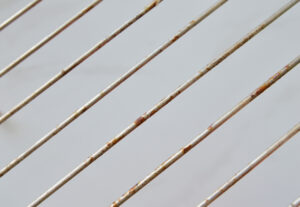