3D printing has revolutionised manufacturing, prototyping, and creative design. While most associate this technology with plastic filaments and resins, metal wire is emerging as a viable material for additive manufacturing. Engineers and designers are increasingly exploring how wire can be integrated into 3D printing to expand its capabilities.
At The Crazy Wire Company, we offer a variety of high-quality metal wires, including stainless steel, titanium, and nichrome, which have potential applications in additive manufacturing. This guide explores the possibilities of using wire in 3D printing, its advantages, limitations, and the best wire types for different applications.
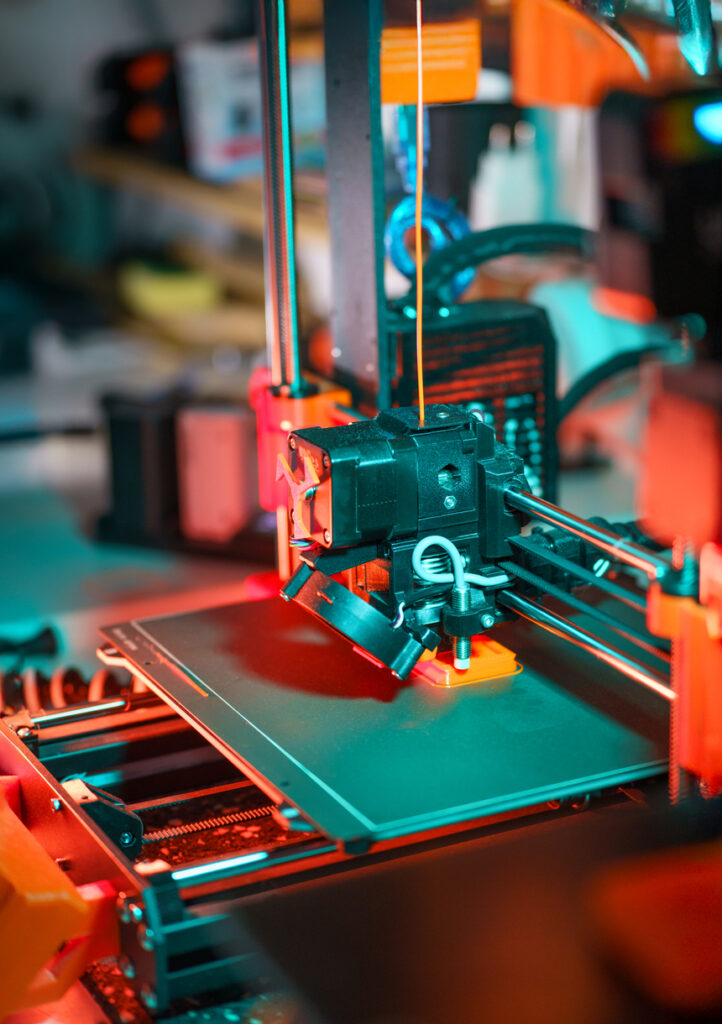
How Can Wire Be Used in 3D Printing?
Wire-based 3D printing is an additive manufacturing process where metal wire is fed through a heated nozzle or an electric arc system, gradually forming a structure layer by layer. There are several techniques where metal wire plays a critical role in the printing process:
✅ Wire Arc Additive Manufacturing (WAAM) – Uses an electric arc to melt metal wire into precise structures.
✅ Laser Wire Deposition (LWD) – Utilises a laser to melt wire, offering precision and control.
✅ Extrusion-Based Wire Printing – Feeds wire through a heated nozzle, similar to Fused Deposition Modelling (FDM)
✅ Hybrid Printing Systems – Combines wire with traditional materials like plastic to reinforce structures.
These methods allow for strong, durable, and highly conductive components suitable for industrial, aerospace, and medical applications.
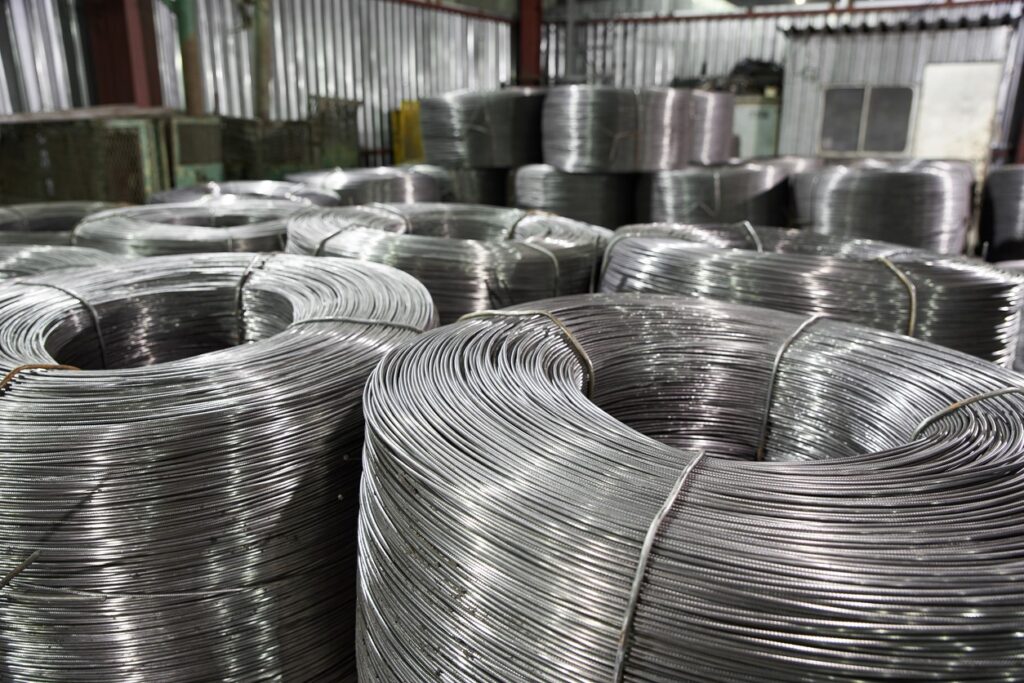
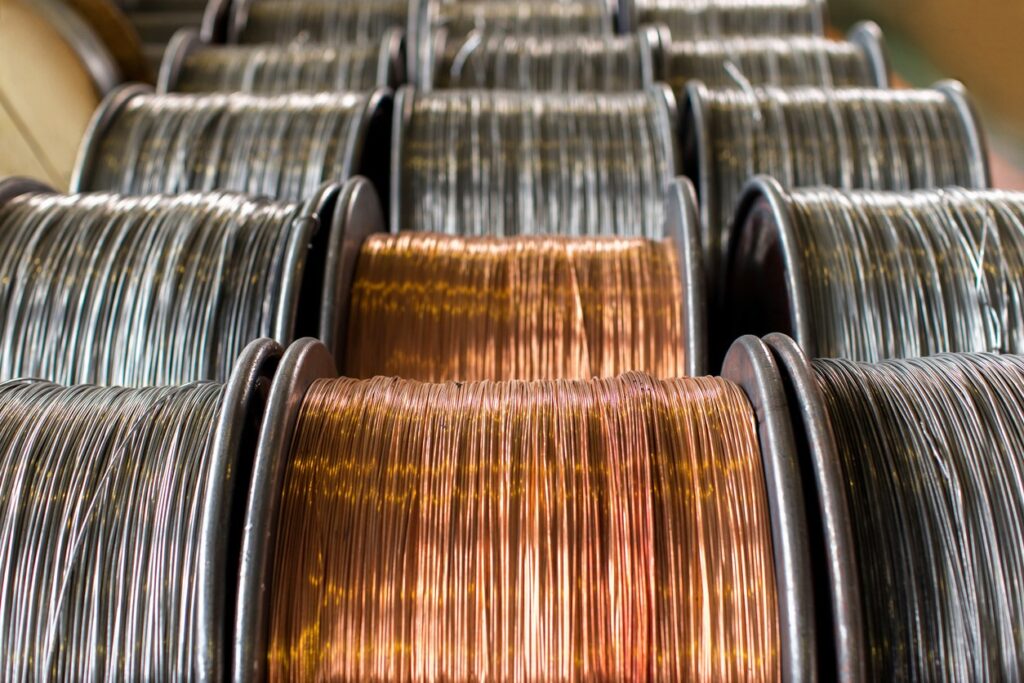
Best Types of Wire for 3D Printing
Not all wires are suitable for additive manufacturing. The right wire type depends on factors such as conductivity, strength, and heat resistance. Below is a comparison of commonly used wires:
Wire Type | Composition | Best Use Case | Strengths |
---|---|---|---|
Stainless Steel Wire | Iron-Chromium-Nickel | Structural printing, aerospace | High strength, corrosion-resistant |
Titanium Wire | Pure Titanium | Medical implants, lightweight structures | Biocompatible, excellent strength-to-weight ratio |
Nichrome Wire | Nickel-Chromium | Heating elements, electronic applications | High heat resistance, durable |
Aluminium Wire | Pure Aluminium | Lightweight components, prototyping | Lightweight, good conductivity |
Copper Wire | Pure Copper | Conductive parts, electronic circuits | Excellent electrical conductivity |
✅ Tip: Stainless steel and titanium wires are widely used in industrial-grade metal printing for their strength and resistance to corrosion.
Advantages of Using Wire in 3D Printing
✔ Material Efficiency – Wire-based printing minimises waste compared to traditional subtractive manufacturing.
✔ High Strength-to-Weight Ratio – Metals like titanium and stainless steel provide robust structures with minimal material use.
✔ Cost-Effective – Wire-based systems can be more affordable than metal powder alternatives.
✔ Customisation – Wire-fed printing allows for custom shapes and designs with high precision.
✔ Sustainability – Reduced material waste makes this method environmentally friendly.
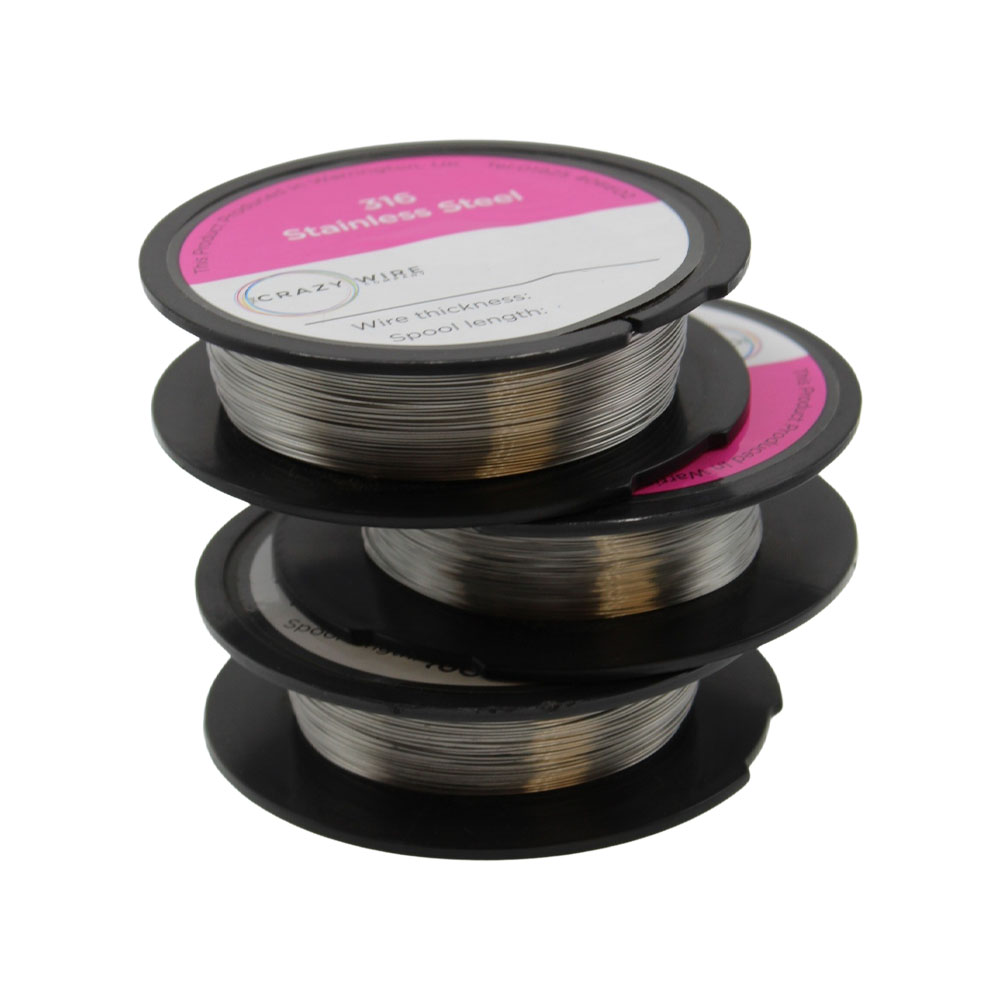
These advantages position wire as a promising alternative for various industries, including aerospace, medical, and automotive manufacturing.
Challenges and Limitations
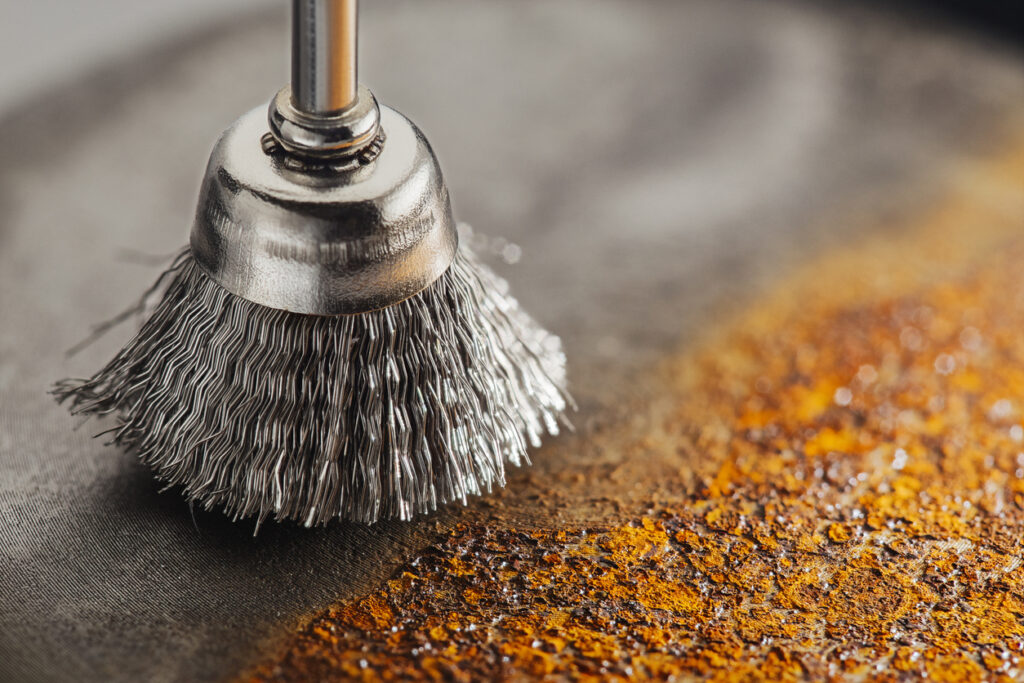
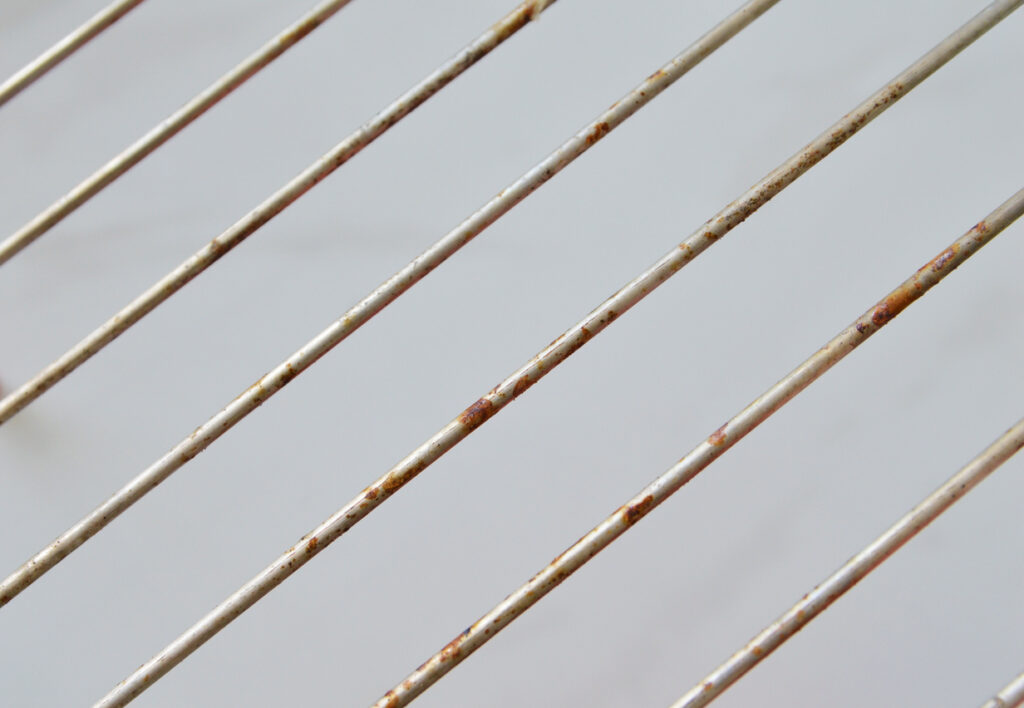
Despite its potential, wire-based 3D printing comes with challenges that must be addressed:
Higher Energy Consumption – Processes like WAAM require substantial energy to melt metal wire.
Limited Material Compatibility – Not all wire types can be effectively printed due to varying melting points and flow properties.
Surface Finish Limitations – Wire-fed printing may result in rougher textures compared to powder-based metal printing.
Equipment Costs – Initial investment in wire-based additive manufacturing systems can be high.
Nevertheless, advances in technology continue to address these challenges, making wire-fed printing more accessible.
Applications of Wire in Additive Manufacturing
Wire-based additive manufacturing has broad applications across different sectors. Below are some of the most common areas where this technology is making an impact:
1. Aerospace & Automotive
Lightweight yet strong components for engines, aircraft parts, and structural reinforcements.
Rapid prototyping for designing and testing new materials before large-scale production.
2. Medical Industry
Biocompatible titanium wire is used to create customised implants and prosthetics.
Dental applications benefit from strong yet lightweight wire-based frameworks.
3. Industrial Tooling
Rapid manufacturing of high-strength tools and spare parts.
Repair and refurbishment of worn-out components using wire-fed deposition.
4. Electronic and Electrical Components
Conductive wire printing enables the creation of electronic circuits and heat-resistant electrical components.
Customised copper wire parts for advanced electrical applications.
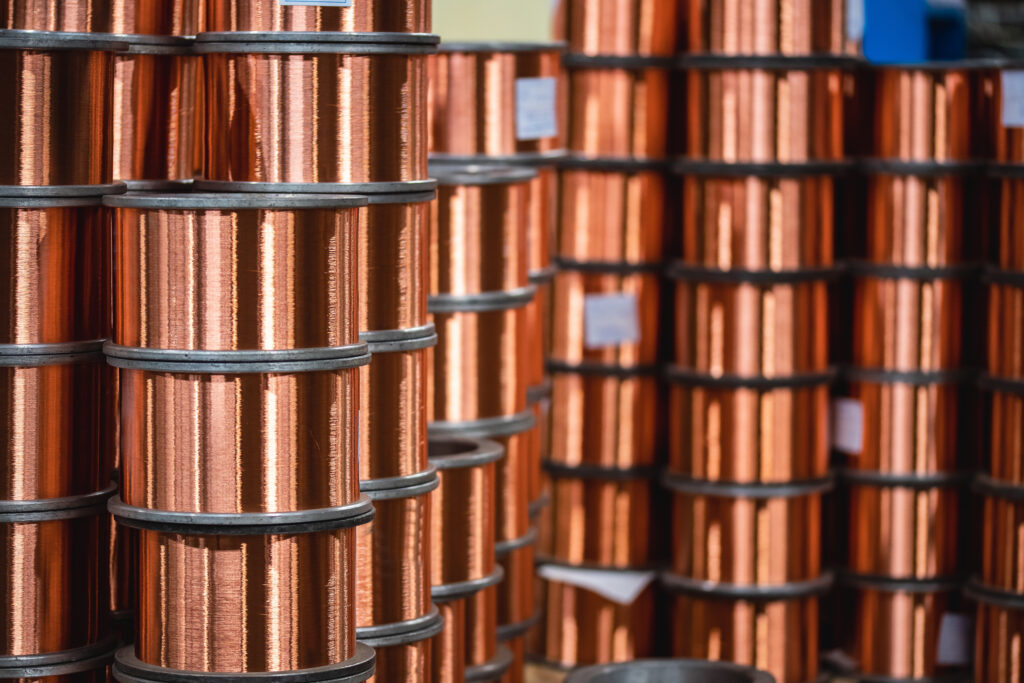
Graph: Comparison of Wire-Based and Powder-Based Metal Printing
A comparative graph showing the differences between wire-based and powder-based metal printing in terms of cost, material efficiency, energy consumption, and surface finish can illustrate the trade-offs between these methods.
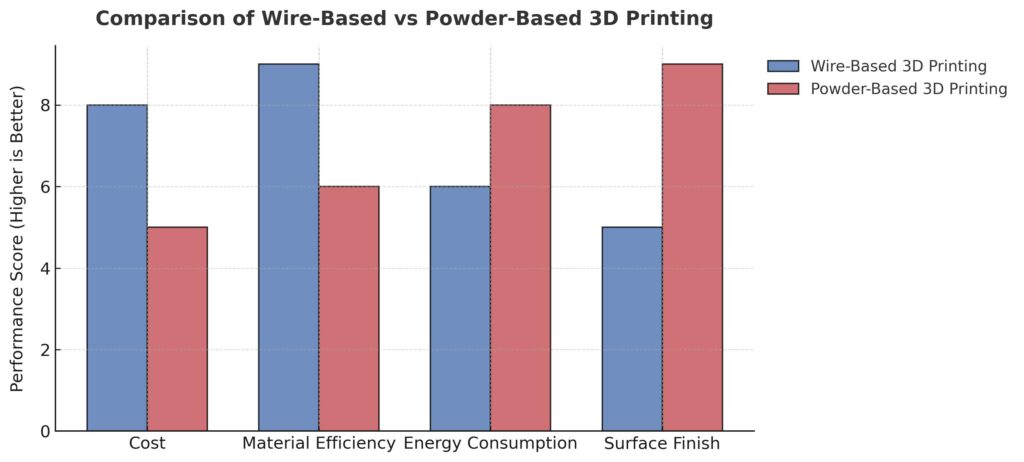
(Graph comparing material waste, production speed, and precision between wire-fed and powder-based additive manufacturing.)
✅ Key Insight: Wire-based 3D printing is more material-efficient and cost-effective, while powder-based methods offer finer surface finishes.
Future of Wire in 3D Printing
As technology advances, wire-based additive manufacturing is expected to grow. Research and development efforts are focused on:
Improving print resolution and precision
Developing hybrid 3D printers that integrate both wire and powder materials
Enhancing automation and AI-driven manufacturing
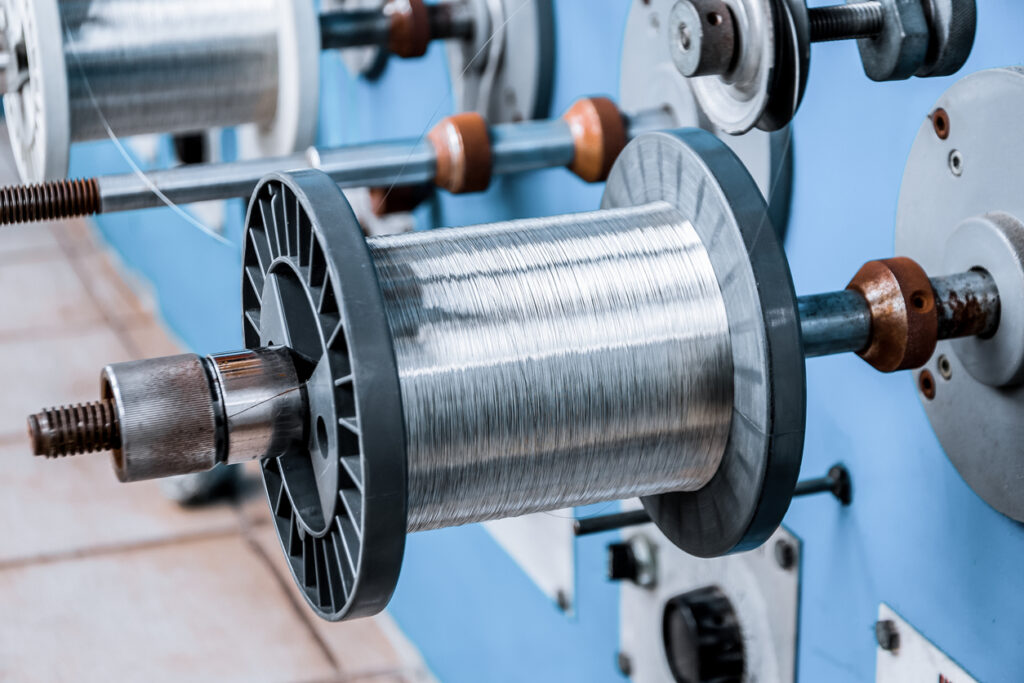
The increased adoption of metal wire in 3D printing could revolutionise industries that demand strong, lightweight, and customisable components.
Why Buy High-Quality Wire from The Crazy Wire Company?
At The Crazy Wire Company, we provide premium-grade wire materials suitable for 3D printing and other advanced applications:
✔ Stainless steel and titanium wire for high-strength prints.
✔ Nichrome wire for heat-resistant applications.
✔ Copper and aluminium wire for conductive and lightweight parts.
✔ Fast UK dispatch with expert advice on wire selection.
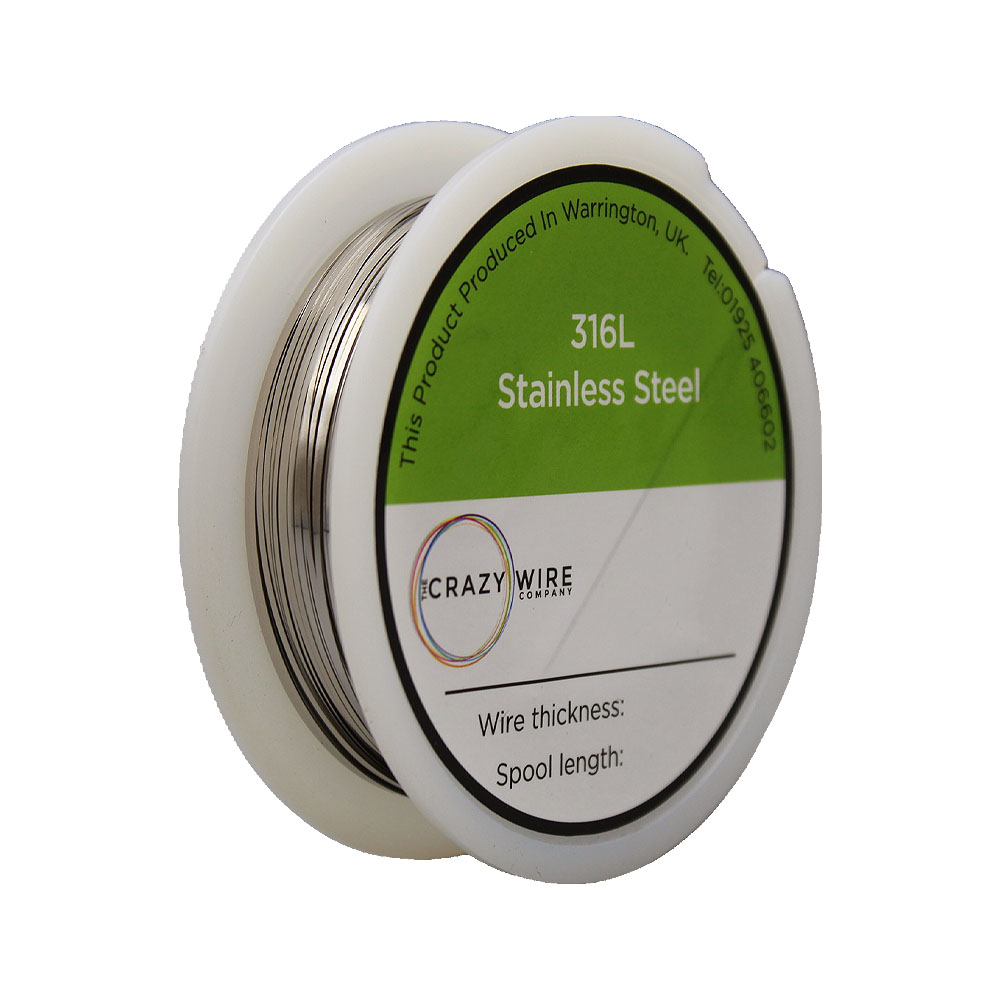
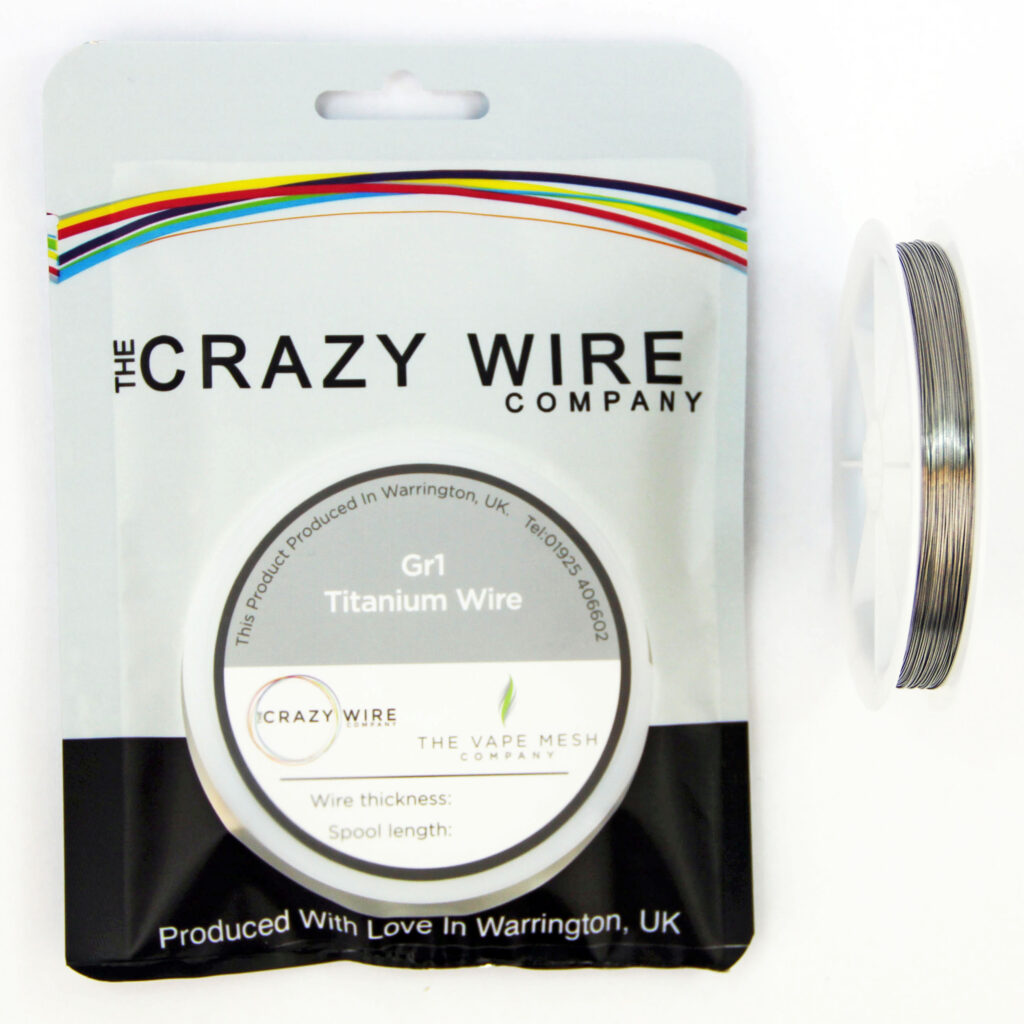
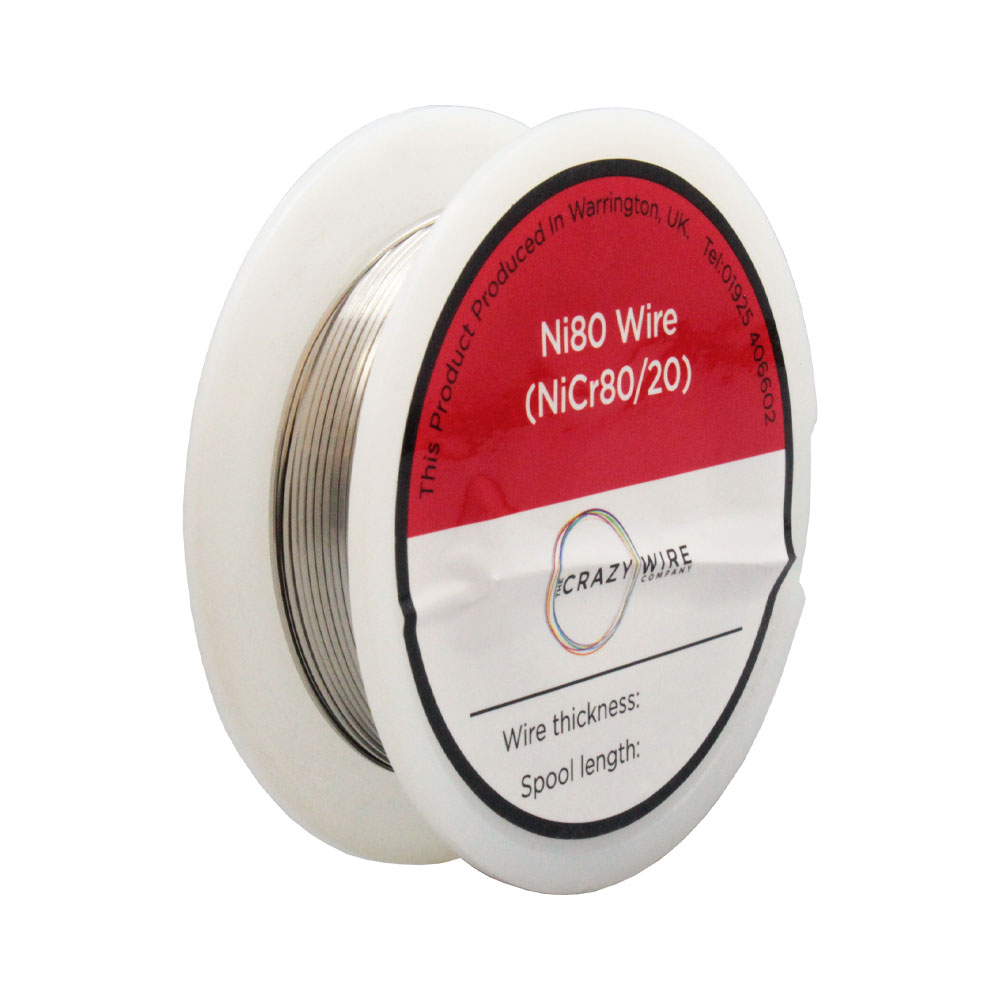
Conclusion: Is Wire a Viable Material for 3D Printing?
Wire-fed 3D printing presents exciting opportunities in manufacturing, offering strength, efficiency, and sustainability. While challenges exist, ongoing advancements are making wire-based additive manufacturing more accessible. Stainless steel, titanium, and copper wires are among the best options for those looking to integrate metal wire into their additive manufacturing projects.
For the best selection of high-quality wire for advanced applications, explore our full range at The Crazy Wire Company today!
Shop Now for Premium Wire Materials!
We offer also a massive range of stainless steel wire and nichrome wire through our store. Choose the wire that you want to work with and we’ll get spooling.
If you’re interested in learning more about wire, check out our other blog on Everything You Need to Know About Wires.
We are also proud to supply this product on our highly popular eBay store, check us out there too.
Thank you for checking out our site.
- MULTIBUY SAVINGS – ORDER 5 FOR 20% OFF
- FREE UK Delivery For All Orders Over £25
- Immediate Express Dispatch From Stock
- Orders Fulfilled From Warrington, UK
- Tracked Delivery with Order Updates
- 30-Day Unused Returns Accepted
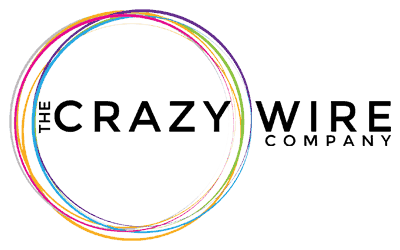