In the world of welding, the choice of wire is as crucial as the skill of the welder.
Stainless steel MIG (Metal Inert Gas) wire is a staple in welding applications, known for its strength, versatility, and corrosion resistance.
This wire type is central to achieving durable and clean welds in a variety of projects. However, in the quest for the perfect welding material, a question arises: Can 304 grade round wire, renowned for its wide-ranging applications and robustness, serve as a viable alternative to traditional stainless steel MIG wire?
This exploration delves into the technicalities and practicalities of using 304 grade stainless steel wire in MIG welding, examining its properties, performance, and suitability for this specialised task.
Let’s go…
Understanding Stainless Steel MIG Wire
In MIG welding, also known as Gas Metal Arc Welding (GMAW), stainless steel MIG wire is specifically designed. As the wire passes through the welding gun, it melts and forms the weld pool, joining two metal pieces by providing filler material. The MIG welding of stainless steel wire is commonly used in automotive, construction, and food processing equipment projects that require strong, corrosion-resistant welds.
The suitability of a wire for MIG welding is determined by several key characteristics:
- Composition: Typically, the alloy mix in the wire should include elements such as chromium, nickel, and molybdenum to ensure compatibility with the metals being welded.
- Strength: It is vital that the wire is strong enough so that it will be able to create a weld that will be able to withstand various stresses without breaking or deforming.
- Melting Point: The melting point of the metal must be suitable to ensure smooth feeding through the welding gun and proper fusion with the base metal.
Overview of 304 Grade Stainless Steel Wire
304 grade stainless steel, also known as A2 stainless steel, is the most commonly used stainless steel alloy in the world, appreciated for its excellent blend of properties.
- Composition: As a result of its composition, which consists of approximately 18% chromium and 8% nickel, this alloy is known for its high corrosion resistance, which makes it suitable for use in a wide range of environments.
- Corrosion Resistance: As a result of the high chromium content in the metal, a passive layer of chromium oxide is formed on the surface of the metal, protecting the metal from rust and other corrosive attacks.
- General Uses: A wide range of applications, such as kitchen equipment, architectural paneling, chemical containers, and various types of hardware, rely heavily upon 304 stainless steel due to its durability and resistance to a wide range of temperatures and environmental conditions.
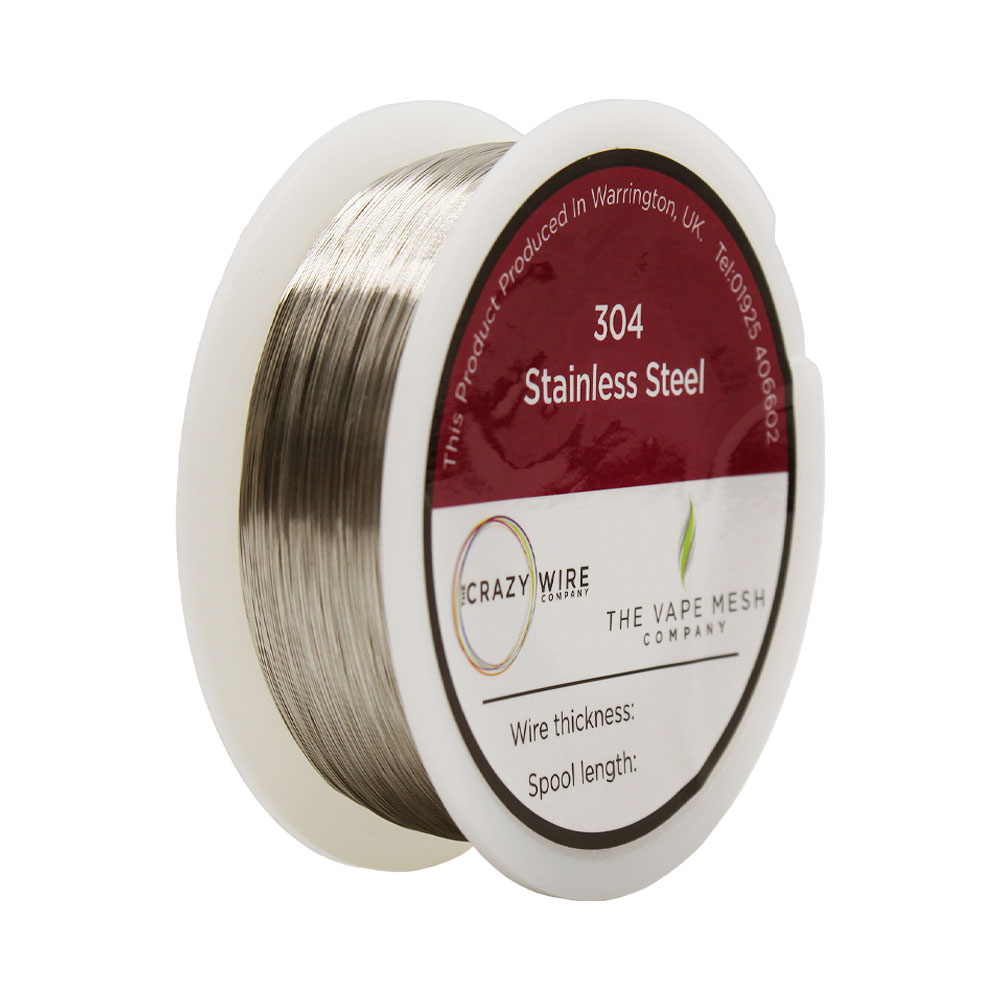
Comparing 304 Grade Wire and Standard MIG Wire
In order to determine whether 304 grade round wire is a suitable alternative to standard stainless steel MIG wire, it is imperative to compare their characteristics:
Chemical Makeup:
- 304 Grade Wire: It is predominantly composed of 18% chromium and 8% nickel. Known for its excellent corrosion resistance and good mechanical properties, this composition is known for its excellent corrosion resistance.
- Standard MIG Wire: For MIG welding, stainless steel MIG wires, such as ER308, ER309, and ER316, are typically used, each with specific alloy compositions tailored to match specific base metals.
Physical Properties:
- 304 Grade Wire: A widely known product that is known for its durability and resistance to a wide range of temperatures and environmental conditions. There is, however, an important thing to keep in mind when working with this type of material. It’s usually not made with welding applications in mind.
- Standard MIG Wire: Designed specifically for welding, these wires have controlled amounts of elements like silicon, manganese, and carbon, which aid in the welding process, ensuring smooth feeding through the welding gun and proper fusion with base metals.
Performance in Welding:
- 304 Grade Wire: Although it is corrosion resistant, it may not perform as well as standard MIG wire in terms of flow, fusion, and spatter control.
- Standard MIG Wire: This product is specifically designed for MIG welding, providing consistent flow, optimal fusion with base metals, and minimal spatter.
Potential Benefits and Drawbacks
Benefits:
- Availability: 304 grade wire is widely available and can be a more readily accessible option in some cases.
- Cost-Effectiveness: In certain cases, it may be more cost-effective to use a general-purpose MIG wire than a specialised MIG wire, especially in cases where the special advantages of specialised MIG wires are not required.
Drawbacks:
- Welding Performance: As a result, there may be challenges associated with welding performance, including problems associated with wire feed, arc stability, and spatter control.
- Durability Concerns: It is possible that welds made with 304 grade wire might not be as durable or resistant to corrosion as those made with standard MIG wire.
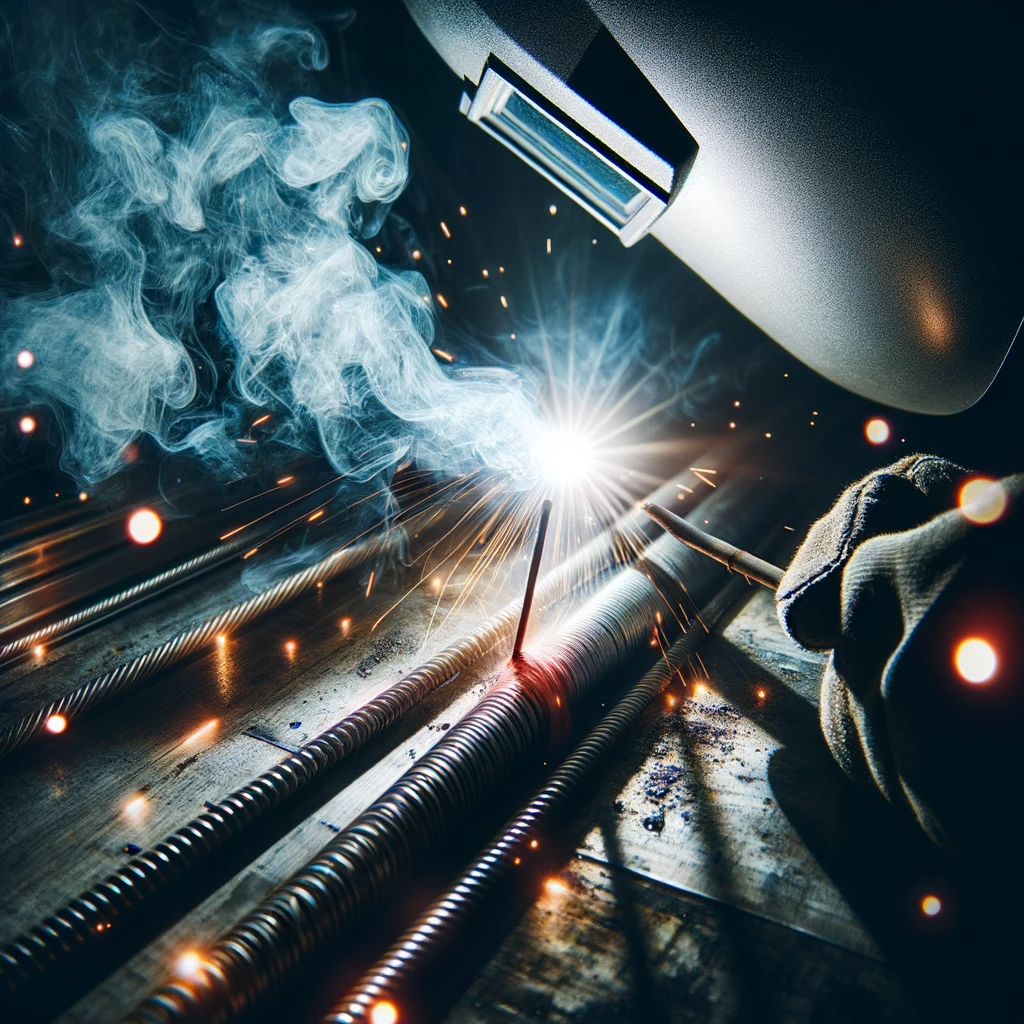
Expert Opinions and Industry Standards
There is no doubt that welding professionals often emphasise the importance of using the right wire for the right job when it comes to welding. To ensure optimal results, it’s generally recommended to use wire specifically designed for MIG welding, even though 304 grade wire might be used in certain welding scenarios.
As a general rule, welding wire that is manufactured and tested for welding applications usually meets industry standards and guidelines. The purpose of these standards is to ensure that the wire will perform reliably during and after the welding process, regardless of the conditions it will encounter.
There is a degree of debate around the feasibility of using 304 grade wire in MIG welding, with some professionals advising caution and recommending it for applications that are less critical and do not require the specific advantages of standard MIG wire.
Real-World Examples
One notable example of 304 grade wire being used in MIG welding is in a motorcycle workshop. Wire grade 304 was used to weld stainless steel parts of a custom exhaust system. The decision was based on the wire’s immediate availability and cost-effectiveness. In terms of appearance and initial hold, the welds were satisfactory. Over time, the welds exhibited signs of corrosion, causing durability concerns. Choosing the right material for the job is essential, especially in applications requiring long-term reliability.
A small-scale artist created welded stainless steel sculptures using 304 grade wire. Due to its flexibility and availability, wire was an attractive option. The artist noted that the wire performed satisfactorily in creating the art pieces, but there were some challenges in achieving consistent weld quality when compared to standard MIG wire.
The exploration into the use of 304 grade round wire as an alternative to standard stainless steel MIG wire reveals that while it may offer some advantages like availability and cost-effectiveness, it also comes with notable drawbacks, especially in terms of welding performance and long-term durability. Due to its specialised composition and properties designed for welding, standard MIG wire is generally better suited to most welding projects than 304 grade wire. Each welding project requires a different type of material, so it is always advisable to select the most suitable one.
Visit our website to discover a comprehensive range of welding wires and related products if you’re interested in learning more about welding and exploring various wire options. We offer expert advice and high-quality solutions tailored to your specific welding needs, whether you’re a professional welder or a DIY enthusiast.
Find the perfect welding materials for your next project by contacting us today.
We offer also a massive range of stainless steel wire and nichrome wire through our store. Choose the wire that you want to work with and we’ll get spooling.
If you’re interested in learning more about wire, check out our other blog on Everything You Need to Know About Wires.
We are also proud to supply this product on our highly popular eBay store, check us out there too.
Thank you for checking out our site.
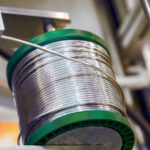
Nichrome Wire Safety: Top Tips for Working Safely
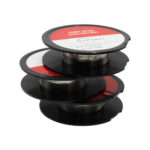
Best Wire for Electronics Projects
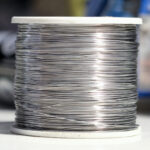
Is Ni80 Wire Suitable for DIY Heating Elements
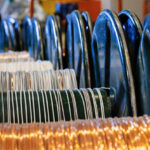
Wire Grades Explained
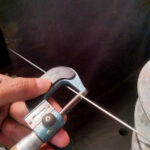
How Wire Diameter Affects Strength and Flexibility
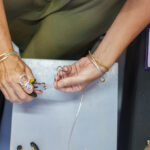
How to Cut and Shape Wire for Custom Applications
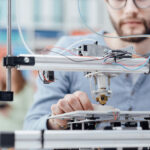
Can Wire Be Used in 3D Printing?
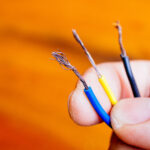
How Wire Composition Affects Conductivity
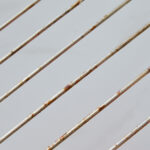