The ability to crimp stainless steel wire is essential for anyone involved in the fabrication or assembly of wire systems, as it provides a robust solution for making durable and reliable connections.
Proper crimping ensures that components stay connected under a variety of conditions, whether for industrial machinery, marine applications, or artistic creations.
The purpose of this guide is to explain the crimping process, presenting a step-by-step method designed specifically for stainless steel wire. With these techniques, you can create strong, corrosion-resistant, and wear-resistant connections for your projects.
Let’s get into it…
Understanding Stainless Steel Wire
Stainless steel wire offers a unique set of properties that make it suitable for a wide range of applications. Crimping is affected by its notable strength and resistance to deformation. Stainless steel maintains its shape and integrity even when subjected to high forces, making it ideal for connections that need to last. In addition, its corrosion resistance ensures that these connections remain secure in environments where lesser materials would degrade.
As a result of these properties, stainless steel wire is preferred in a variety of fields. It is used in industrial settings for machinery and equipment that require longevity and reliability. Marine applications require corrosion resistance to withstand harsh, saltwater conditions. Stainless steel wire is even favoured in the arts for sculptures and jewellery due to its durability. Selecting the right crimping approach is crucial for ensuring the integrity of the wire and the security of the connection based on these properties.
Tools and Materials for Crimping Stainless Steel Wire
Crimping stainless steel wire requires a set of specialised tools and materials, each selected to complement the wire’s properties. The essential tools include:
Crimpers: To properly secure the wire within the connector without damaging it, you need a high-quality crimping tool. To ensure compatibility, choose crimpers designed specifically for stainless steel wire.
Dies: They are used with the crimping tool to shape the crimp connector around the wire. For a snug fit, the die must match the connector size and wire gauge.
Crimp Connectors: These metal sleeves are used to join two pieces of wire together or attach a wire to a terminal. Selecting the right connector size and type is vital for a strong connection.
In addition to these tools, the materials used alongside stainless steel wire during crimping play a significant role.
- Sleeves and Terminals: In addition to being constructed from stainless steel materials, these components are designed to withstand the same environmental conditions as the wire itself, ensuring that the connection remains strong over time as it is exposed to the elements.
Stainless steel wire offers strength, reliability, and resistance to environmental challenges when you choose the appropriate tools and materials for the job.
Preparing the Wire for Crimping
A successful crimp starts long before the actual crimping action; it begins with meticulous preparation of the stainless steel wire. A proper preparation ensures the wire is in optimal condition for crimping, which is essential for a durable and reliable connection. For proper crimping of stainless steel wire, follow these steps:
Cutting: To cut stainless steel wire to the desired length, use a wire cutter. A jagged edge can make it difficult to insert the wire into the crimp connector properly, so make sure the cut is clean and straight.
Stripping: Use a wire stripper designed for stainless steel if your wire has a protective coating or insulation. You should avoid nicking the wire strands, as this can compromise its strength.
Cleaning: After cutting and stripping the wire, clean it to remove any oils, dirt, or residues. Clean wires ensure better contact with connectors. When necessary, use a mild solvent that does not leave a residue and a non-abrasive cloth.
Straightening: If the wire has been coiled or bent, straighten it. You can do this by gently pulling the wire through a cloth. A straight wire is easier to work with and ensures a better fit in the connector.
This preparation phase is crucial; taking the time to properly prepare the wire can significantly impact the quality of the crimped connection.
Step-by-Step Crimping Process
Crimping stainless steel wire requires precision and attention to detail. Follow these steps for a secure crimp:
Positioning the Wire and Connector: The prepared wire should be inserted fully into the crimp connector or terminal. Make sure the wire is seated deeply and evenly within the connector. Make sure the strands of stranded wire are neatly gathered and not splayed.
Positioning the Crimper: Ensure that the connector (with the wire inserted) is positioned according to the crimper’s instructions. Crimping should hold the connector securely without crushing it.
The Crimping Action: Crimp the connector onto the wire by firmly pressing the crimper’s handles together. Make sure the connector is evenly crimped around the wire by applying consistent pressure.
Inspection: Check the connection after crimping. An appropriately crimped connector will have a uniform deformation around the crimp area without any sharp edges or gaps. The wire should not pull out from the connector with a moderate tug.
Tips for a Secure and Neat Crimp:
- Use the correct die size for the connector being crimped.
- Do not attempt to crimp the connector more than once, as this can weaken the connection.
- For critical applications, consider using a crimping tool with a built-in ratchet mechanism that ensures the correct pressure is applied.
The final step is to inspect the crimped connection. You should see a smooth, uniform compression around the connector. The wire or connector material should not appear overly compressed or damaged. Crimped connections can be confirmed by a visual inspection followed by a gentle tug test.
Troubleshooting Common Crimping Issues
Crimping stainless steel wire can sometimes lead to challenges, but most issues can be addressed with the right knowledge and approach. Here are some common crimping problems and their solutions:
Incomplete Crimp: The crimp connector may not fully compress around the wire if the die size or force are incorrect. When crimping, use the correct tools and apply sufficient pressure.
Damaged Wire: The wire can be damaged by over-crimping, reducing its structural integrity. After crimping, if the wire is visibly damaged or has sharp edges, it’s best to cut it and start again. Over-crimping can be prevented by using a calibrated crimping tool.
Loose Connection: If a connector isn’t crimped tightly enough, it can cause a loose connection. It usually occurs when the crimper isn’t calibrated properly or the wrong die size is used. Replace the connector and crimp again, ensuring proper tool settings, if possible.
Corrosion: Stainless steel is resistant to corrosion, but the crimp connector might not be. Using connectors made from or coated with corrosion-resistant materials compatible with stainless steel can mitigate this issue.
If a crimp is found to be defective upon inspection-whether incomplete, damaged, or loose-the safest solution is to remove the defective crimp, prepare the wire again, and perform a new crimp with fresh components. As a result, the connection is reliable and safe.
Testing and Verifying Crimped Connections
Testing the integrity of crimped connections is crucial, particularly in applications where failure could lead to significant consequences. Here are some methods for testing crimped connections on stainless steel wire:
Visual Inspection: Begin with a thorough visual check for uniform compression and absence of damage.
Tug Test: Gently but firmly pull on the wire and connector to test the mechanical strength of the crimp. The connection should not separate or show signs of weakness.
Continuity Test: Use a multimeter to verify electrical continuity through the connection. This can also help detect any increase in resistance that might indicate a poor crimp.
Resistance Measurement: For critical applications, measuring the resistance of the crimped section compared to an uncrimped section can reveal differences in electrical conductivity, indicating the quality of the crimp.
High Voltage Test: In applications where the wire will be exposed to high voltages, a high voltage test ensures that the insulation and the crimp can withstand the operating conditions.
Regular testing and verification are key to ensuring long-term reliability. For applications where failure is not an option, conducting periodic inspections and tests can help identify potential issues before they lead to significant problems.
Advanced Crimping Techniques for Specific Applications
To ensure the integrity and reliability of stainless steel wire connections, advanced crimping techniques may be required. As an example, in the aerospace industry, where safety is paramount, double crimping with specialised dies can provide additional security. Using heat-shrink crimp connectors in marine applications can offer extra protection against corrosion and moisture in harsh environments.
Medical devices often require micro-crimping tools that can accurately crimp stainless steel wires, ensuring precision and reliability. Additionally, in the automotive industry, high-volume crimping tools that deliver consistent results quickly are essential.
In order to choose the right crimping technique, you need to understand the specific requirements of your industry and application. Crimping solutions are tailored to meet every need, whether it’s ensuring ultra-reliable connections in critical systems or achieving high throughput in manufacturing.
The skill of crimping stainless steel wire requires attention to detail and an understanding of the material’s properties. Creating durable and reliable connections starts with selecting the right tools, preparing the wire, and crimping and testing it. You can approach crimping confidently, knowing that you have the knowledge to succeed.
You can find a wealth of resources and products on The Crazy Wire Company’s website if you are interested in learning more about stainless steel wire and its applications.
Whether you need high-quality stainless steel wire, specialised crimping tools, or expert advice, we’re here to help. Don’t hesitate to contact us and discover how we can support your projects.
We offer also a massive range of stainless steel wire and nichrome wire through our store. Choose the wire that you want to work with and we’ll get spooling.
If you’re interested in learning more about wire, check out our other blog on Everything You Need to Know About Wires.
We are also proud to supply this product on our highly popular eBay store, check us out there too.
Thank you for checking out our site.
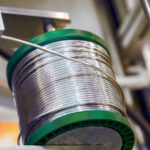
Nichrome Wire Safety: Top Tips for Working Safely
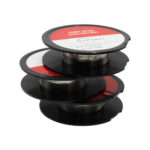
Best Wire for Electronics Projects
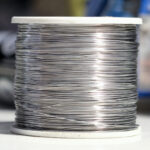
Is Ni80 Wire Suitable for DIY Heating Elements
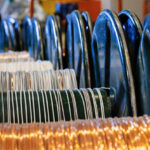
Wire Grades Explained
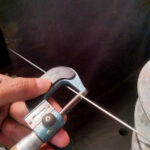
How Wire Diameter Affects Strength and Flexibility
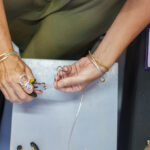
How to Cut and Shape Wire for Custom Applications
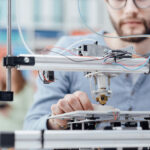
Can Wire Be Used in 3D Printing?
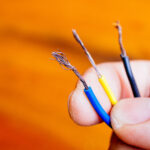
How Wire Composition Affects Conductivity
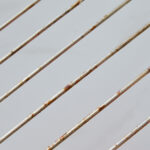