In the diverse world of materials, a common question arises: “Is 316 Stainless Wire Conductive?” This query is not just for academic interest but is a crucial consideration for engineers, designers, and fabricators who rely on the conductive properties of metals for a vast array of applications. The answer to this question affects decisions in fields ranging from construction to electronics, where the material’s performance can significantly impact the efficiency and safety of a project. In this discussion, we will explore the electrical conductivity of 316 stainless steel wire—a material known for its corrosion resistance and strength—and examine its suitability for electrical applications. This examination will shed light on how 316 stainless steel wire stands up against other conductive materials and what users can expect in terms of performance and application.
What is 316 Stainless Steel Wire?
316 stainless steel wire is an austenitic chromium-nickel alloy known for its exceptional corrosion resistance and strength. The addition of molybdenum (typically 2-3%) to the basic composition of 18% chromium and 8% nickel enhances its corrosion resistance, particularly against chlorides and industrial solvents. This makes it an ideal material for use in harsh environments where exposure to corrosive elements is a concern.
While often selected for its mechanical properties and resistance to corrosion, 316 stainless steel wire’s electrical conductivity is comparatively lower than that of many other metals used in electrical applications. Despite this, the material does conduct electricity and can be used in situations where its other properties are required, and high conductivity is not the primary concern.
Electrical Conductivity of 316 Stainless Wire
The electrical conductivity of a material is a measure of its ability to conduct an electric current. In the case of 316 stainless steel wire, its conductivity is significantly lower than metals like copper or aluminum, which are commonly used in electrical applications. Specifically, 316 stainless steel has an electrical conductivity of about 2.5% to 6.5% of that of pure copper, depending on the exact alloy composition and processing methods.
When compared to pure metals, the alloying elements in stainless steel, such as chromium, nickel, and molybdenum, introduce scattering centers for the electrons, thereby reducing the material’s conductivity. However, this does not preclude its use in electrical applications altogether. It may still be suitable for uses where other properties, like temperature stability, strength, and corrosion resistance, are more important than the material’s ability to conduct electricity.
Understanding the relative conductivity of 316 stainless steel wire is crucial when specifying materials for electrical applications. It may not be the first choice for applications where low resistance and high conductivity are required, but it certainly has a place where its comprehensive profile of properties can be leveraged.
Factors Influencing 316 Stainless Wire's Conductivity
The conductivity of 316 stainless steel wire is influenced by a variety of factors, with the alloy composition being a primary determinant. The presence of alloying elements like chromium, nickel, and molybdenum, which enhance corrosion resistance and mechanical properties, also impede the flow of electricity. These elements disrupt the crystalline structure that facilitates the free flow of electrons, thereby reducing conductivity.
Another factor is the diameter, or gauge, of the wire. In general, thicker wires have a lower resistance and hence better conductivity than thinner wires due to a greater cross-sectional area for the electrons to traverse. However, since 316 stainless is not as conductive as materials like copper, even changes in wire diameter will not bring its conductivity close to that of these more conductive metals.
Temperature also plays a role; as temperature increases, the resistance of metallic conductors typically increases due to the intensified vibration of the lattice ions, which scatter the electrons more effectively. For 316 stainless steel wire, this means that its already limited conductivity can decrease further as the operating temperature rises.
Example Calculation for 316 Stainless Steel Wire Conductivity:
Consider a 1mm diameter 316 stainless steel wire at room temperature. To calculate its resistance, we first need to know its resistivity (ρ), which is a material constant.
The resistance (R) can be calculated using the formula:
R = ρ × (L / A)
where:
- L is the length of the wire,
- A is the cross-sectional area of the wire, which can be calculated based on the diameter of the wire.
For a 1mm diameter wire, the cross-sectional area (A) is derived from the formula for the area of a circle (A = π × r2), noting that the radius (r) is half the diameter.
Given the diameter of 1mm (or a radius of 0.5mm), converting to meters (since resistivity is often in ohm-meters), we have a radius of 0.0005 meters. Thus, the area would be:
A = π × (0.0005)2
Substitute the values of ρ, L, and A into the resistance formula to find the resistance of the wire.
For a wire with a specified length, increasing the diameter (thereby increasing the area A) will result in a decrease in resistance, which in turn, could improve conductivity.
Applications of 316 Stainless Wire in Electrical Projects
Despite its relative conductivity, 316 stainless steel wire finds practical uses in various electrical projects. Its superior corrosion resistance makes it an excellent choice for outdoor applications or in environments prone to corrosive substances where other materials would fail quickly.
For example, 316 stainless steel wire can be used in the maritime industry, where saltwater corrosion is a concern. It may also be used for supports, framework, or enclosures for outdoor electrical applications where exposure to the elements is inevitable.
Another scenario where 316 stainless wire is preferred involves applications where the wire must maintain structural integrity at elevated temperatures, which might be encountered in industrial heating systems. Although the wire doesn’t primarily serve as a conductor in these cases, its ability to conduct electricity safely at high temperatures can be leveraged for internal connections that require corrosion resistance as well as a modest degree of conductivity.
In the field of instrumentation and control systems, 316 stainless steel wire is often used for its strength and durability, even if it requires larger diameters or additional wires to compensate for its lower conductivity. The trade-off for better mechanical and chemical properties is deemed worthwhile in these specialized applications.
Comparing 316 Stainless Wire to High-Conductivity Wires
When it comes to conductivity, 316 stainless steel wire and high-conductivity wires like copper or aluminum operate in different leagues. Copper, with its superior electrical conductivity, is the standard by which other materials are often compared. It’s widely used for the majority of electrical wiring because of its low resistivity, which is approximately 1.68 x 10^-8 ohm-meters. Aluminum, while not as conductive as copper, still offers a good balance of conductivity and weight, making it suitable for power distribution applications.
In contrast, 316 stainless steel’s electrical resistivity is much higher, and therefore its conductivity is significantly lower. Where high conductivity is essential, such as in power transmission or electronics, copper or aluminum would be the preferred choice. However, when environmental factors such as exposure to corrosive substances or extreme temperatures come into play, 316 stainless steel becomes a contender due to its resistance to corrosion and ability to maintain structural integrity.
Choosing the right wire requires assessing the specific needs of the application. If the environment is harsh, but the electrical load is light, 316 stainless might be appropriate. For heavy electrical loads or where efficient energy transfer is crucial, copper or aluminum would be more suitable.
Maximizing the Efficacy of 316 Stainless Wire in Conductive Applications
While 316 stainless steel wire may not be the first choice for conductive applications, its efficacy can be maximized with the right strategies:
Wire Treatment: Certain treatments can slightly improve the conductivity of 316 stainless wire, such as annealing, which can reduce internal stresses and resistance.
Insulation: High-quality insulation can help prevent energy loss, especially if the wire operates in an environment where temperatures fluctuate.
Correct Gauge: Selecting a larger gauge wire can help to offset the lower conductivity of 316 stainless steel, as a thicker wire will have a lower resistance.
Understanding the conductive properties of 316 stainless steel wire is essential for making informed decisions in electrical project planning. While it may not match the conductivity of materials like copper or aluminum, its resistance to corrosion and high-temperature performance make it invaluable in certain scenarios.
To explore the extensive properties and potential applications of 316 stainless steel wire, visit The Crazy Wire Company’s website. Our team is ready to provide you with expert advice to select the best wire for your project needs, combining our extensive knowledge with a wide selection of high-quality wire options. Reach out to us to ensure your projects benefit from the exceptional properties of 316 stainless steel wire.
We offer also a massive range of stainless steel wire and nichrome wire through our store. Choose the wire that you want to work with and we’ll get spooling.
If you’re interested in learning more about wire, check out our other blog on Everything You Need to Know About Wires.
We are also proud to supply this product on our highly popular eBay store, check us out there too.
Thank you for checking out our site.
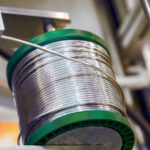
Nichrome Wire Safety: Top Tips for Working Safely
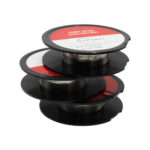
Best Wire for Electronics Projects
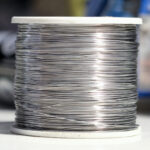
Is Ni80 Wire Suitable for DIY Heating Elements
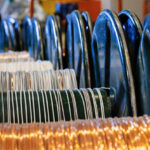
Wire Grades Explained
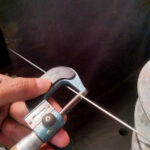
How Wire Diameter Affects Strength and Flexibility
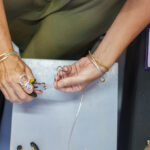
How to Cut and Shape Wire for Custom Applications
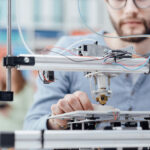
Can Wire Be Used in 3D Printing?
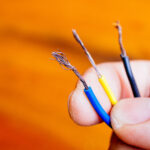
How Wire Composition Affects Conductivity
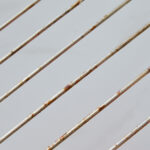