FeCrAl vs Nichrome Wire
When it comes to choosing the right wire for heating elements and electrical applications, the debate often narrows down to two popular contenders: FeCrAl (Iron-Chromium-Aluminum) and Nichrome (Nickel-Chromium).
These materials are renowned for their resistance to oxidation, high melting points, and durability, making them ideal for a range of uses from industrial heating systems to household appliances like toasters and hair dryers. But which one truly stands the test of time? In this comprehensive comparison, we’ll dive deep into the durability of FeCrAl vs Nichrome wire, exploring every aspect from material properties to real-world applications, to help you make an informed decision.
Material Properties
Composition: Nichrome, an alloy of nickel and chromium, occasionally contains iron and other elements to enhance its ductility and resistance to oxidation. Its unique composition makes it highly resistant to electric current, generating heat efficiently when voltage is applied.
FeCrAl, on the other hand, includes iron, chromium, and aluminum. The presence of aluminum significantly enhances the alloy’s resistance to oxidation and corrosion, especially at high temperatures, making it an excellent choice for heating elements in harsh conditions.
Melting Point: The melting point of a material is crucial for its performance, especially in high-temperature applications. Nichrome boasts a melting point of approximately 1400°C (2552°F), which makes it suitable for many heating applications.
FeCrAl alloys, however, have melting points that can reach up to 1500°C (2732°F), providing a slight edge in applications requiring higher temperature resistance. This higher melting point contributes to the durability and lifespan of FeCrAl-based components, making them a preferred choice in industrial settings where extreme conditions are common.
Electrical Resistance: Electrical resistance is a fundamental property for materials used in heating elements. Nichrome provides a stable and high resistance, which translates to efficient heat generation with less material.
FeCrAl offers a higher resistance per unit length, which can be beneficial in reducing power consumption and improving the efficiency of heating appliances.
The choice between the two often depends on the specific requirements of the application, including the desired temperature range and efficiency.
Resistance to Oxidation and Corrosion
Mechanisms of Oxidation: At high temperatures, materials oxidize, affecting their performance and lifespan. Nichrome forms a protective oxide layer that shields the wire from further oxidation, maintaining its integrity under thermal stress.
FeCrAl alloys benefit from the addition of aluminum, which forms an even more robust alumina layer (Al2O3) that offers superior protection against oxidation. This characteristic is particularly advantageous in environments where the wire is exposed to high temperatures and potentially corrosive elements.
Corrosion Resistance: In addition to high-temperature resistance, corrosion resistance is critical for materials used in environments exposed to potentially corrosive substances. Nichrome’s composition provides good resistance to corrosion, making it suitable for various applications.
However, FeCrAl’s aluminum content not only enhances its high-temperature oxidation resistance but also its performance in corrosive environments, offering an extended lifespan in harsher conditions.
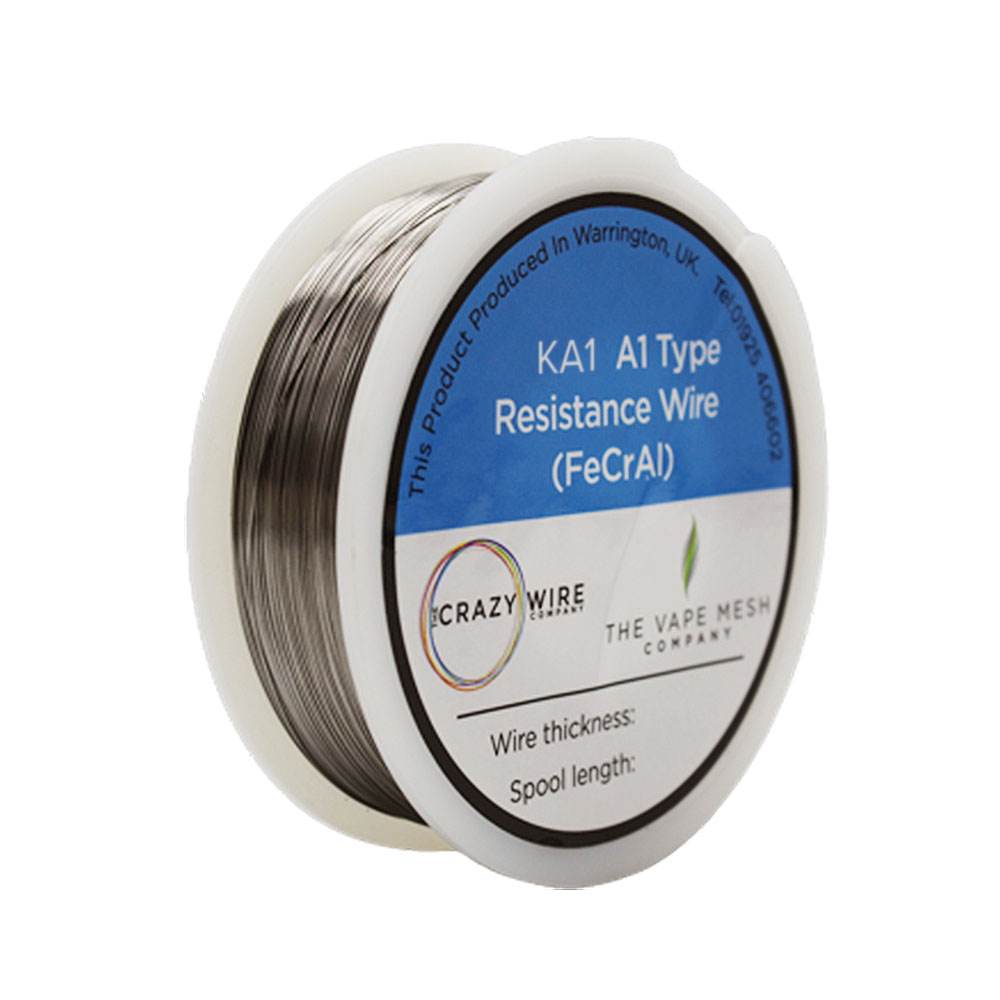
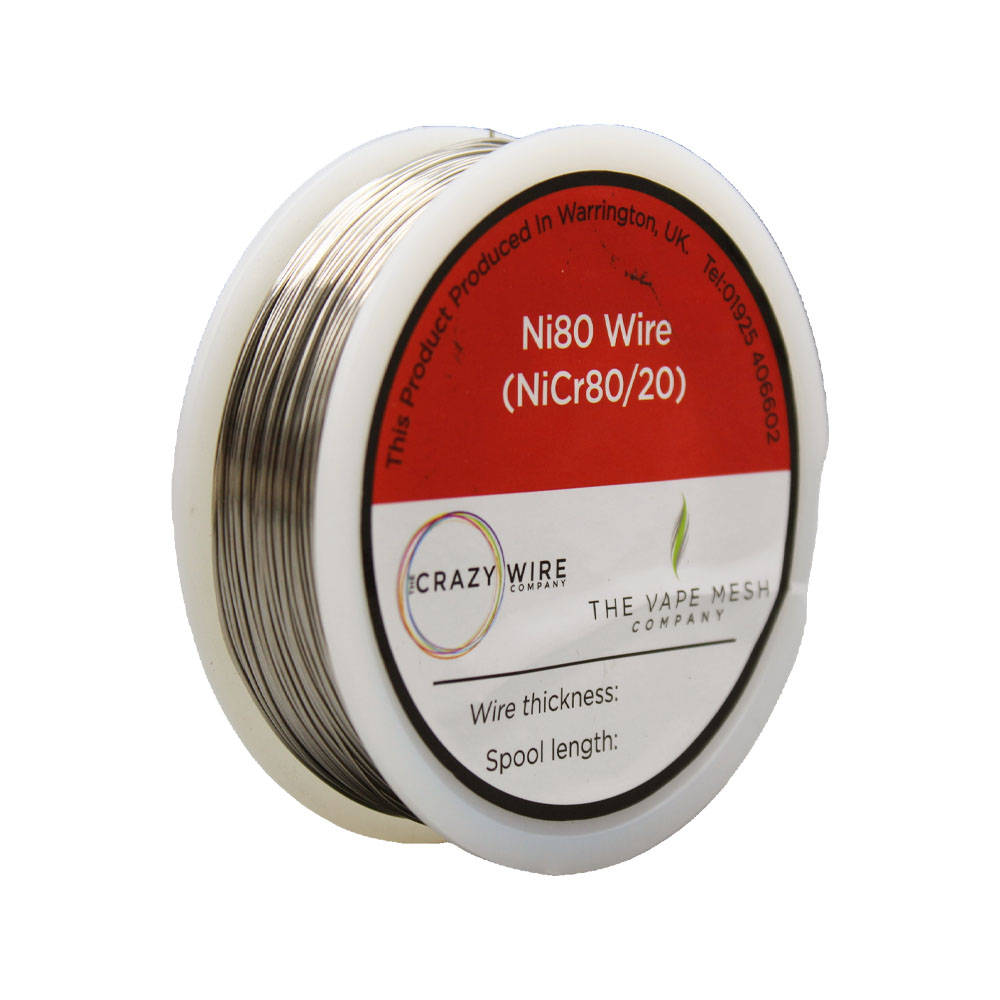
Thermal Expansion and Stability
Coefficient of Thermal Expansion: The coefficient of thermal expansion is a measure of how much a material expands when heated. A lower coefficient is generally preferable for materials used in applications where stability and precision are critical.
FeCrAl alloys typically have a lower coefficient of thermal expansion compared to Nichrome, meaning they experience less dimensional change with temperature fluctuations. This stability is essential for applications requiring precise tolerances and can significantly affect the durability and reliability of heating elements.
Thermal Stability: Repeated heating and cooling cycles can cause materials to degrade over time. Nichrome’s structure offers good thermal stability, resisting changes in shape and maintaining its electrical resistance well over time.
FeCrAl’s combination of elements provides exceptional thermal stability, allowing it to withstand continuous cycling between extreme temperatures without significant degradation. This makes FeCrAl an excellent choice for applications where the material is subject to frequent temperature changes.
Applications and Real-World Use
Industrial Applications: In industrial settings, the choice between FeCrAl vs Nichrome wire often comes down to the specific requirements of the application. Nichrome’s reliability and efficiency in moderate-temperature applications make it a popular choice for industrial heaters, hot wire cutters, and resistors.
FeCrAl’s superior high-temperature performance and resistance to oxidation and corrosion make it ideal for use in industrial furnaces, kilns, and heating elements exposed to harsh conditions.
Consumer Appliances: In consumer appliances, such as toasters, hair dryers, and ovens, Nichrome wire has been the traditional choice due to its effective heat generation and durability.
However, FeCrAl is gaining popularity for its longer lifespan and ability to withstand higher temperatures, making it an increasingly common choice for manufacturers looking to improve the durability and performance of their products.
Specialized Uses: Each material also finds specialized uses that leverage its unique properties. For example, Nichrome is used in fireworks and model rocket igniters due to its ability to heat up rapidly.
FeCrAl is preferred in applications requiring prolonged exposure to extremely high temperatures, such as in certain types of industrial heating elements and aerospace components, where its higher temperature resistance and stability are crucial.
Here’s a table outlining the pros and cons of FeCrAl vs Nichrome wire:
Feature | FeCrAl Wire | Nichrome Wire |
---|---|---|
Composition | Iron, Chromium, Aluminum | Nickel, Chromium, (sometimes Iron) |
Melting Point | Higher (up to 1500°C) | Lower (about 1400°C) |
Electrical Resistance | Higher resistance per unit length, reducing power consumption | Stable and high resistance, efficient heat generation with less material |
Resistance to Oxidation | Excellent, due to aluminum content forming a robust alumina layer | Good, forms a protective oxide layer |
Corrosion Resistance | Superior, especially in harsh conditions | Good, suitable for various applications |
Coefficient of Thermal Expansion | Lower, less dimensional change with temperature fluctuations | Higher, more susceptible to dimensional change with temperature |
Thermal Stability | Exceptional, withstands continuous cycling between extreme temperatures without significant degradation | Good, resists changes in shape and maintains electrical resistance well |
Applications | Preferred for high-temperature industrial applications, furnaces, kilns | Widely used in consumer appliances, industrial heaters, moderate-temperature applications |
Cost-Effectiveness | Generally more cost-effective in the long term due to durability | Initially less expensive but may have higher lifetime costs due to lower temperature thresholds |
Environmental Impact | Aluminum content may increase environmental impact during production | Relatively lower environmental impact during production |
By considering the specific needs of each application, including temperature requirements, environmental conditions, and desired lifespan, engineers and designers can choose the most appropriate material—whether Nichrome or FeCrAl—to ensure optimal performance and durability.
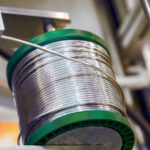
Nichrome Wire Safety: Top Tips for Working Safely
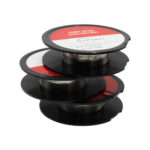
Best Wire for Electronics Projects
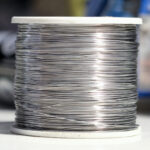
Is Ni80 Wire Suitable for DIY Heating Elements
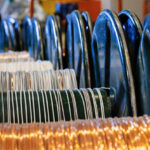
Wire Grades Explained
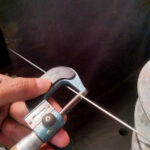
How Wire Diameter Affects Strength and Flexibility
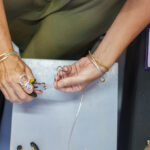
How to Cut and Shape Wire for Custom Applications
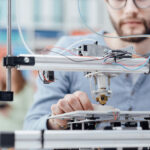
Can Wire Be Used in 3D Printing?
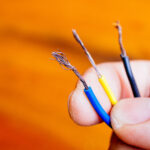
How Wire Composition Affects Conductivity
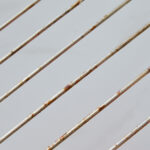
The Science Behind Wire Oxidation: Which Wires Resist Corrosion Best?
We offer also a massive range of stainless steel wire and nichrome wire through our store. Choose the wire that you want to work with and we’ll get spooling.
If you’re interested in learning more about wire, check out our other blog on Everything You Need to Know About Wires.
We are also proud to supply this product on our highly popular eBay store, check us out there too.
Thank you for checking out our site.