In the intricate world of wired coil technology, the innovation race never truly stops.
Over time, enthusiasts and professionals alike have developed various coil configurations, each promising a unique blend of performance, durability, and efficiency.
Among the vast array of options available, two coil types have managed to stand out prominently: the Flapton and the Clapton.
This article delves deep into the similarities, differences, and potential applications of these two coil designs.
Let’s begin…
A Brief Introduction to Coil Technology
Before diving into the specifics, it’s vital to understand the significance of coil design.
Coils, in many applications, play a pivotal role in ensuring efficient energy transfer. The design, material, and craftsmanship of a coil can significantly impact its performance and the overall experience of the user.
Clapton Coils: The Classic Design
Named after the resemblance to guitar strings, Clapton coils are a perennially popular choice among coil enthusiasts the World over.
The design is relatively straightforward, involving a core wire tightly wrapped with a thinner wire.
Features of Clapton Coils:
- Layered Design: The defining feature of Clapton coils is the layered structure, with the core wire serving as the primary conductor and the outer wire enhancing the surface area.
- Versatility: Clapton coils can be made using various materials, making them adaptable to different needs.
- Consistent Performance: The simple design ensures a steady and predictable output, making them a reliable choice for many applications.
Flapton Coils: The Modern Twist
The Flapton coil can be seen as a refined version of the Clapton coil.
Instead of a round wire wrap, the Flapton utilizes a flat wire to encase the core, leading to an increased surface area.
Features of Flapton Coils:
- Enhanced Surface Area: The flat wire wrap ensures a larger surface area compared to the traditional Clapton, which can lead to better energy distribution.
- Efficient Heat Dissipation: The design of the Flapton promotes even heat distribution, reducing the chances of hotspots.
- Flexible Configurations: Flapton coils can be tailored to specific needs by adjusting the thickness of the core and wrap wires.
Comparing the Two: Advantages and Limitations
1. Surface Area & Performance: Flapton coils generally have a more significant surface area due to their flat wire wrap, potentially providing better energy distribution and efficiency. However, the difference might not always be stark, depending on the exact specifications of the coils compared.
2. Durability: While both designs are robust, the Flapton’s flat wire wrap might offer slightly better durability due to the even heat distribution. The layered design of Clapton coils, on the other hand, might be more susceptible to wear and tear in the long run.
3. Craftsmanship & Complexity: Crafting a perfect Clapton coil is an art in itself. The process involves precision and patience. Flapton coils, with their added complexity of using flat wire, can be even more challenging to perfect, requiring a higher level of craftsmanship.
4. Versatility & Use Cases: Both coil types are highly versatile, suitable for various applications. Their efficiency and design make them a popular choice for scenarios requiring consistent energy transfer and output.
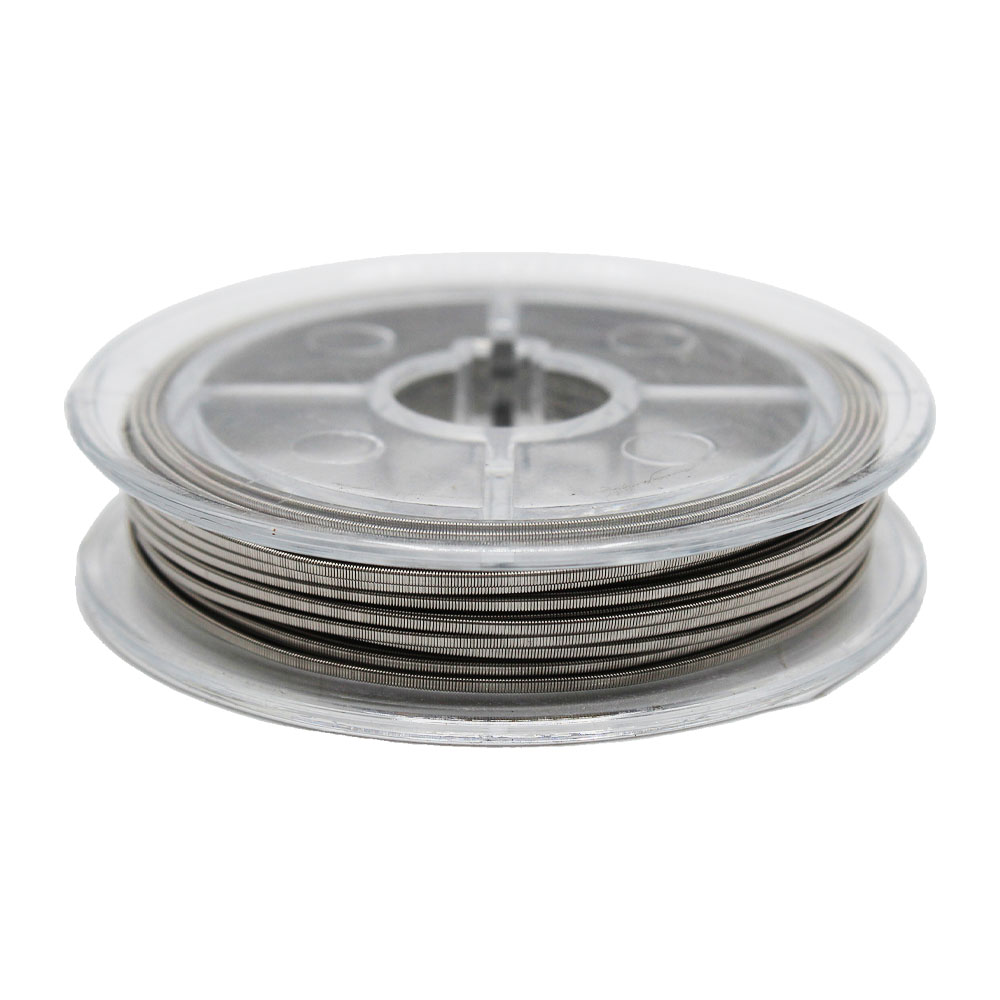
Can I Create My Own?
Absolutely! Crafting a Flapton wire requires precision, patience, and the right materials. Let’s delve into the process of building a Flapton wire.
Materials Required:
- Core Wire: This is the main wire around which the outer wrap is wound. It is generally thicker than the wrap wire and will serve as the primary conductor.
- Flat Wire (Ribbon Wire): This is the wire you’ll wrap around the core wire. It’s called “flat” or “ribbon” because of its flattened cross-section, which provides the characteristic surface area of the Flapton.
- Wire Cutters: For cutting the wires to the desired length.
- Drill: This tool will help you wrap the flat wire around the core wire with precision.
- Swivels: They help keep the core wire straight while wrapping.
- Pliers: Useful for holding wires and ensuring tightness.
Steps to Build a Flapton Wire:
- Preparation: Cut a length of your core wire, roughly about 12-15 inches or based on your requirement. This ensures you have ample length to work with and account for any mistakes.
2. Setting Up the Drill:
- Insert one end of the core wire into the chuck of the drill and tighten it.
- On the other end, attach the wire to a swivel, which should be clamped or fixed to a steady surface. This setup ensures that the core wire remains straight during the wrapping process.
3. Starting the Wrap:
- Take the flat wire (ribbon wire) and manually wrap it around the core wire near the drill chuck. This initial wrapping ensures the flat wire holds onto the core wire before you start the drill.
- Make sure the wraps are close together and tight. This initial manual wrapping is crucial for a good start.
4. Drilling:
- Holding the end of the flat wire with pliers (or by hand with tension), start the drill slowly, allowing the flat wire to wrap around the core wire.
- Keep consistent tension on the flat wire. This ensures even spacing and tightness.
- The swivels will allow the core wire to rotate freely, ensuring the wrap is consistent.
5. Progress & Patience:
- As you progress, make sure the wraps are close together and there are no overlaps or gaps.
- If you notice any inconsistencies, you can reverse the drill a bit and fix the wrap. Remember, patience is crucial. Don’t rush the process.
6. Finishing Up:
- Once you’ve wrapped the desired length, stop the drill and cut off the excess flat and core wires using wire cutters.
- Inspect your Flapton wire for any imperfections. If there are any sections with overlaps or gaps, you can either fix them manually or cut them off.
Building a Flapton wire is a skill that requires patience and practice, but the satisfaction of creating a perfectly wrapped wire is worth the effort.
This is a simple guide into how this can be done. Please conduct all relevant research before attempting to create and use any form of coil wire.
Choosing between Flapton and Clapton coils boils down to individual preferences and specific needs. If you’re looking for a classic design with proven performance, Clapton coils might be the way to go. However, if you’re seeking a modern twist with a potentially larger surface area and efficient heat distribution, Flapton coils could be worth the exploration.
Both designs have carved a niche for themselves in the coil community, reflecting the ever-evolving nature of coil technology. As innovations continue to emerge, it’s exhilarating to ponder what the future holds for these intricate marvels of engineering. One thing is for certain: the quest for the perfect coil design is a journey that’s far from over.
We offer also a massive range of stainless steel wire and nichrome wire through our store. Choose the wire that you want to work with and we’ll get spooling.
If you’re interesting in learning more about wire, check out our other blog on Everything You Need to Know About Wires.
We are also proud to supply this product on our highly popular eBay store, check us out there too.
Cheers
Chris & The Crazy Wire Team
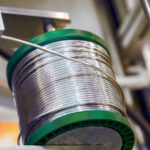
Nichrome Wire Safety: Top Tips for Working Safely
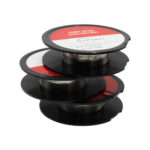
Best Wire for Electronics Projects
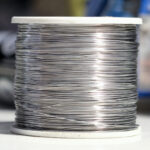
Is Ni80 Wire Suitable for DIY Heating Elements
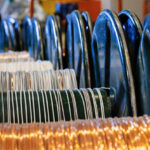
Wire Grades Explained
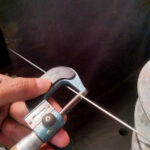
How Wire Diameter Affects Strength and Flexibility
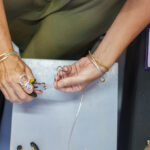
How to Cut and Shape Wire for Custom Applications
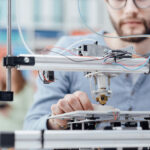
Can Wire Be Used in 3D Printing?
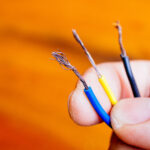
How Wire Composition Affects Conductivity
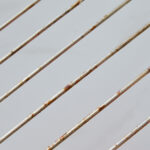